Offset Printing
manroland EcoLogic: Economy through Ecology
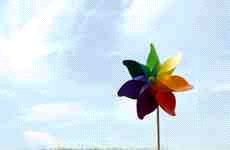
Saturday 07. June 2008 - Environmental protection anchored in corporate strategy
Companies that protect resources by reducing waste and emissions save a lot of money. Efficient energy management reduces operating costs, improves working conditions, and protects the environment. Ecology and economy are not contradictory concepts: manroland printing presses combine environmental protection and efficiency.
manroland exemplifies its own research. The press manufacturer has received multiple recognitions for its standards in environmental protection. manroland was awarded the 2007 Glanzlicht-Auszeichnung (“Highlight Award”) by the Minister for the Environment in the German state of Hesse for its reduction of energy consumption at the Offenbach/Mainhausen production site. This reduction was achieved in
conjunction with increased sales and higher productivity. Consumption values have been decreasing since 2001 – energy by 30 percent, natural gas by 38 percent, and water by 32 percent. The figures speak for themselves: economy and ecology are not mutually exclusive. Whether in web or sheetfed offset, manroland is continually working on press concepts in order to optimize procedures and resource
consumption. In addition to conservation of resources, manroland also focuses on reducing waste and emissions as well as increasing energy efficiency.
Protecting resources
In addition to paper (which is the most-used resource in a printing press), other materials such as inks, coatings, or washing agents are needed for the printing process. manroland also offers solutions for efficient use of resources in these areas. Due to its special polymer coating, the ink fountain coating system QuickChange Surface considerably simplifies the process of slicing out ink residue and subsequent
cleaning on sheetfed presses. Less washing agents and cleaning rags, and no special ink fountain foil are necessary. Ink residue is reduced to a minimum with ROLAND SelectInkSupply: supply from cartridges ensures minimal filling levels in the ink fountains, and ink is only replenished where it is actually needed. Quick ink changes and up to 65 percent less ink residue are thus made possible.
Reducing waste
With QuickStart manroland has developed a patented system for ink presetting in web offset that produces saleable copies after just a few cylinder revolutions. QuickStart Pro minimizes start-up waste even further. Among others, the Kieler Nachrichten profits from this system, producing newspapers with only 75 start-up waste copies. In the sheetfed sector, QuickChange solutions reduce start-up and
production run waste. QuickChange Color comprises several functions, including a self-learning function for ink-slide presetting.
Lowering emissions
The Pressedruck media group in Augsburg, Germany, uses a COLORMAN, XXL, as the XXL presses from manroland print more economically. Combined with its innovative groundwater cooling system, energy consumption has been reduced by 27 percent in comparison with the old system, despite a 12.7 percent increase in printed paper. manroland’s “emission approved” certificate from the
Berufsgenossenschaft Druck und Papierverarbeitung (BGDP – German professional organization for printing and paper processing) proves that especially lowemission operation is also possible for sheetfed presses. manroland’s emissions are considerably lower than the EC Directive statutory and recommended maximum values for emissions of dampening solution (IPA), cleaning agents, ink mist, coating, printing powder, and noise.
Saving energy
Direct drive has been established in the web offset sector. Compared to conventional drives, modern direct drives are characterized by a higher degree of efficiency. This reduces energy loss from around 20 percent to 7 percent. Printing press units, such as dryers, dampening solution cooling devices, and blowers, use up most of the required energy. Energy consumption can be lowered significantly through new solutions. The ROLAND SelectCombiCenter combination device for dampening solution cooling and inking unit temperature control implements an integrated free-cooling function for inking units that is capable of providing cooling performance in the temperature control circuit for more than 70 percent of the year without using the cooling unit. The drying process uses up most of the energy measured compared to a press’s overall consumption. manroland developed the
ROLAND SelectDryer IR/TL for the ROLAND 900, XXL series in order to optimize
dryer energy consumption in large-format sheetfed offset printing. This includes optional
drying air heat recovery that works in combination with proven individual adjustment
of the drying function through infinitely variable control. Up to 30 percent
of energy is saved as a result.
Printing alcohol-free
This year at drupa manroland will present its environmental competency at an ecology InfoPoint where customers can receive comprehensive consultation regarding ecological and economical printing production. At the printservices service counter, experts provide information on upgrading press components, and at printcom, you can receive information on ecologically smart process-compliant system
components for e.g. IPA-free printing. manroland also uses alcohol-free production methods on all sheetfed printing presses.