Packaging
OYSTAR sets hygiene standards
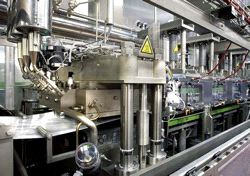
Wednesday 12. November 2008 - Industry-specific requirements call for innovative solutions
Hygiene is the decisive factor in the manufacture of foodstuffs and pharmaceutical products. OYSTAR. The Process & Packaging Group – the number two among the worlds providers of packaging equipment, technology, services, and process know-how – raises the bar in this area through further developments and innovative technologies. The 17 manufacturing companies in the OYSTAR group draw on decades of experience and implement packaging and cleaning technology for the food, dairy, pharmaceutical, and cosmetics industries to the highest standards of hygiene.
Hygienic packaging for foodstuffs and dairy products
Producers of milk products, baby food, and fruit juices are realizing the benefits of sterilization using steam and pressure. OYSTAR Gasti (Schwäbisch Hall, Germany) offers the DOGASEPTIC cup filling and wrapping machine with the hygiene standards “ultraclean” and “aseptic”, which keep the packaging process free from vegetative micro-organisms or from any micro-organisms (including bacteria spores) respectively. Both hygiene standards are thoroughly secured via a completely closed machine system that protects against recontamination by infected ambient air and offers secure packaging material sterilization by hydrogen peroxide (H2O2).
OYSTAR Hassia (Ranstadt, Germany) aseptic systems use only steam to sterilize foil in form-filling and sealing machines. Steam is already present in most dairy and food processing plants. In contrast to chemicals, steam leaves no residue in the product and is safe for personnel. Campina Deutschland, for example, has turned its back on sterilization with hydrogen peroxide in favor of the steam sterilization process (performed at approx. 150 degrees Celsius) developed by OYSTAR Hassia.
In the USA, OYSTAR Packaging Technologies (Davenport/Iowa) uses the patented MAP (Modified Atmosphere Packaging) method to pack foodstuffs in cans, jars, bottles, vials, pouches, bags, and trays. Air is extracted from the packaging and replaced with gases such as nitrogen, oxygen, and carbon dioxide. The MAP method can be used with foodstuffs and is far superior to traditional methods. Typical atmosphere critical packaging solutions include:
Fresh Foods – Cheese, Ground Beef, Processed Meat & Poultry, Cut Vegetables, and Pasta.
Granular and powders products such as Infant Formula, Evaporated Milk and Coffee.
Edible Oils, Dressings, Dips and Sauces?Snack Foods, Nuts and Seeds
Health Care, Nutritional and Pharmaceutical products
Innovative cleaning solutions for the pharmaceutical industry
OYSTAR provides pharmaceutical companies with solutions that not only meet the stringent hygiene requirements of the manufacturing process, but also ensure efficient cleaning of the packaging equipment. For its clean-in-place procedure with the new and innovative Ultraclean System, OYSTAR Hüttlin (Schopfheim, Germany) has integrated a metal filter into its fluidized bed facilities that opens during cleaning. An internal cone in the filter cartridge is pushed downwards via a piston rod. As soon as the filter opens, solids are quickly rinsed away on the clean gas side. This cuts cleaning time significantly without compromising purity in any way.
With its Wash in Place (WiP) system, OYSTAR Manesty (Liverpool, UK) offers a fully programmable sequence that cleans all substrates using water, detergents, or foam. Residual material is removed from the feeder and flushed automatically, significantly reducing cleaning time. The unique stepped cabinet design reduces the complexity of components to be cleaned. The WiP sequence may also be linked to the cleaning of ancillary equipment such as dedusters and in-process control units.