Finishing & Screen Printing
Amcor invests in BOBST lamination technology to support more sustainable product development
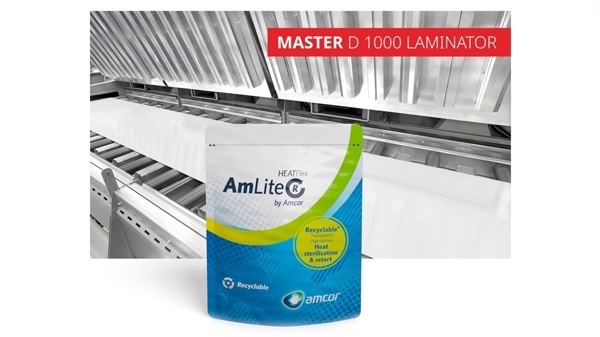
Thursday 08. July 2021 - A new BOBST MASTER D 1000 S multi-technology laminator has been installed at Amcors Sustainability Centre of Excellence in Ghent, Belgium. The machine will be used in the development and testing of new innovative multi-layer product constructions for Amcor worldwide.
Amcors global R&D efforts to manufacture more sustainable flexible packaging is coordinated from its Sustainability Centre of Excellence in Ghent, in Belgium. In 2018, the global packaging leader announced its commitment to make all its packaging products recyclable or reusable by 2025. Along with 250+ other leading manufacturers and brand owners, it has also signed the New Plastics Economy Global Commitment, which aims to eliminate plastic waste and pollution at source.
“Innovative packaging design, improved recycling infrastructure and consumers playing their part is all key to protect the environment. For converters, this means starting from the traditional laminated products, but reaching right across the entire converting process,” said Kris Buysens, Technical Director, Amcor. “We were the first packaging producer in the world to set ourselves a specific target for making all our products recyclable or reusable by 2025. This pledge is driving all our research and development, and to succeed we need to have the most advanced and flexible technology at our disposal.”
The company works with all parts of the value chain, from suppliers and customers to end users, to better understand the carbon footprint of packaging and identify areas for improvement. The versatility, flexibility and high performance of the new BOBST multi-technology laminator will be central to this process.
“The technical laminates that we develop require a stable and repeatable process, where the adhesive can be finely controlled and measured. We also need a machine where multiple adhesive technologies can be employed,” said Kris Buysens. “We chose the BOBST MASTER laminator because it gives us the tools that we need to develop more environmentally friendly products that meet the challenging demands from our customers and end consumers.”
Innovation to drive more sustainable flexible packaging
With over 47,000 employees at 230 sites in 40+ countries around the world, Amcor posts annual sales of US$ 12.5 billion. Tracing its roots back to 1860, the company provides all types of packaging solutions for the food, beverage, pharmaceutical, health, home and personal care, and pet care sectors, along with a range of technical applications.
The Sustainability Centre of Excellence in Ghent was established in 2019 as part of the companys global effort to stay at the forefront of innovation in packaging and succeed in meeting the 2025 pledge.
Amongst the companys many innovations that are already having an impact on the flexible packaging market is the AmLite Recyclable range. These pioneering products completely eliminates the use of metallized layers traditionally used as barriers, making them more easily recyclable. Analysis has shown that the latest generation, AmLite Ultra Recyclable, can reduce a packs carbon footprint by up to 64% in a cradle-to-cradle comparison with foil laminate equivalents. It will allow brands to transfer products to recyclable flexible packaging across a variety of segments, such as coffee, snacks, dry pet food, and home and personal care.
Bespoke equipment developed with BOBST technology
As a part of the laboratory equipment in Ghent, the new BOBST MASTER D 1000 S laminator has been built to Amcors exact specifications. It is a more compact version than the standard models in the range, as there is no need for wide web conversion, and the running speed is lower to accommodate the unique working requirements. The modular, high efficiency drying tunnel features three sections where the temperature can be individually regulated, and the air recycled.
“Although this is a highly productive machine, for our purposes we were not looking for speed but rather technical prowess, accuracy and the flexibility to cover multiple types of applications,” said Kris Buysens. “Our new BOBST MASTER D 1000 S is an evolution of an older BOBST laminator that we have been using successfully since 2001, so we know and trust the technology.”
In order to deliver a next-generation laminator that would suit Amcors very precisely defined and unique needs, BOBST worked closely with the team at the R&D centre in Belgium to configure the new machine.
Supporting each other for the future of packaging
“The choice of BOBST as supplier of this machine was partially based on the relationship and history Amcor has with BOBST, but more importantly, it was based on the technology and the versatility of the machine,” said Kris Buysens.
“We are naturally very proud to support Amcor in their innovative work as they move towards their 2025 pledge to make all their packaging products recyclable or reusable,” commented Nanni Bertorelli, Product Line Manager Coating and Laminating, BOBST “and the MASTER D 1000 S is the perfect fit for producing the types of high-performance applications that Amcor have become known for worldwide.”
“Sustainability is one of the four core pillars of the BOBST future vision of the packaging industry, and we are actively seeking to improve the carbon footprint of our technologies and our manufacturing processes. Working in unison with all parties involved in packaging production is the only way to make a real change and reduce the environmental impact of packaging,” he concluded.