Finishing & Screen Printing
BOBST laminators go from strength to strength
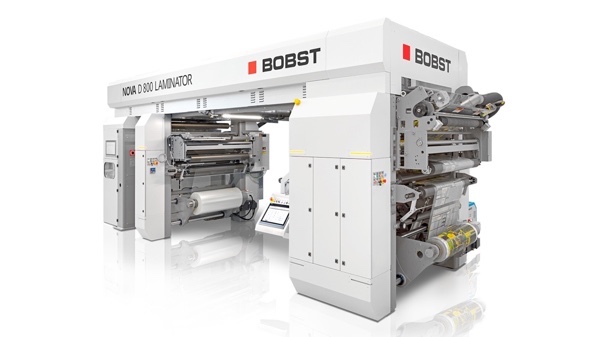
Friday 21. May 2021 - BOBST is shaping a new reality where connectivity, digitalization, automation and sustainability are the cornerstones of packaging production. Those qualities are reflected in the latest additions to BOBSTs laminator portfolio.
These are the latest in a long line of innovative laminating machinery from BOBST. The continued success has quite simply been because the strengths of the equipment are consistent with what is important to users – ease of operation, high performance, low wastage and low impact on the environment.
The BOBST NOVA SX 550 LAMINATOR ticks all the boxes for short order productivity; easy and quick set-up of job parameters within 1 minute; 15 minutes for a complete job changeover; 90 seconds for a transfer roller change; and 5 minutes to complete a fully automatic washing cycle.
It handles a wide range of substrates including paper, alu-foil, metallized films and thin stretchable materials in widths between 1000 and 1500 mm, with a production speed of up to 450 m/min. Tool-less changeovers of transfer rolls are performed within minutes irrespective of whether solid rolls or sleeves types are used.
This provides customers with much-needed flexibility at low cost, which is particularly useful in the current climate, allowing companies to fulfil short orders at short notice. In addition, at a time when time-consuming onsite installations are not ideal, it is a genuine plug and play, machine, meaning it does not require foundations and can be very simply installed in just one week. Configurable with either sleeve or monolithic/integral transfer rollers, it can be used with the majority of your already existing equipment.
Other features contributing to its high productivity include an automatic reel centering system, reducing waste and start-up time, fully integrated automatic washing as standard, and independent setting of thermal regulation for coating unit and metering rolls.
It is also very easy to use, with an intuitive Human Machine Interface (HMI). BOBST NOVA SX 550 is “industry 4.0”-ready for post processing data, also thanks to its fully integrated HMI for setting, display and storage of individual job working parameters. It comes with a patented one-touch automated washing system that requires less cleaning solution compared to similar machines and features an adjustable cleaning cycle of five minutes or less. Its three-column layout enables full accessibility to the laminating nip for quality and process inspection without stopping the machine. And thanks to BOBST adhesive mixer solutions, you can have an effective adhesive quantity control, matching production requirements, while the micrometric adjustment allows perfect coating adhesive distribution.
Meanwhile, BOBST recently extended its range of compact, multi-technology laminating solutions further with the addition of the BOBST NOVA DA 800 LAMINATOR. It is a highly efficient machine delivering optimum performance with all run lengths and types of substrates and adhesive, conventional or designed for recycling. Job changes are simple, fast and without tools for higher machine uptime and fast time-to-market.
Features include the availability of BOBST flexo trolley for high-speed coating of solvent-based adhesive with high solid content, along with unique cost saving performance. The optical and functional qualities of the laminated structures are excellent with all the technologies available: water-based, solvent-based, solventless adhesive lamination, and in-register cold seal, lacquering and additional one color applications.
The machine, available also with automatic winders as BOBST NOVA DA 800 LAMINATOR, is designed to use the same trolleys of BOBST laminators, which are fully interchangeable. With a lamination speed of up to 450 m/min, the multi-trolley design allows for different process technologies such as solvent-based and water-based dry lamination, solventless lamination and in register applications.
BOBSTs unique flexo trolley is ideal for high speed coating of solvent based adhesives with high solid content and cost saving, associated with up to 20% less adhesive used and up to 50% less solvent waste. With its compact design and lateral trolley extraction, the layout enables full accessibility for cleaning and maintenance and allows the operator to easily and rapidly switch between jobs. The fully integrated HMI allows the operator to set, display and store individual job working parameters in easy to recall job recipes. The connectivity features such as apps remote monitoring, downtime tracking and portal lead to a full production and quality control.
Its not just about speed and efficiency, but also superb product quality. The latest trolley design delivers coating uniformity and visual appeal with all applications. It enables perfect web transportation by tunnel motorized rollers, avoiding breakages and scratches on critical substrates like alu-foil and metallized films. A motorized pressure roller ensures more accurate and uniform adhesive metering, ideal for multi-roller and reverse coating technology. And its exclusive Registron Mark-to-Mark reading technology enables optimal in-register cold seal coating and lacquer coating.