Prepress
Know your flow: How an optimized workflow can give your company a competitive advantage
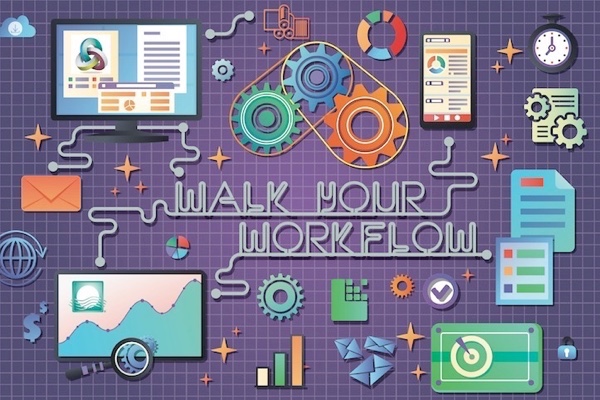
Thursday 15. October 2020 - How well do you really know your workflow? And more importantly, are there untapped opportunities to make it faster and more efficient? Here, Jonathan Malone-McGrew, Senior Director of Engagement at Solimar Systems, explains why it might be time to review your current operations.
To get to know your workflow, first, it is important to define exactly what it means. Put simply, in a print management environment, end-to-end workflow refers to the series of processes that a piece of work passes through right from onboarding to delivery. On top of that, it also includes the ability to track, trace and report on each job
The power of an optimised workflow is the ability to take on more work, push that work through your production processes with minimal interruption or manual intervention, and deliver a quality product to your customers in the shortest time frame possible. However, the needs of any business changes over time, and so workflow efficiency should be regularly reviewed, as what may have worked well for a while may not be delivering efficiencies today. This is especially true of home-grown print workflow management solutions which have evolved to solve urgent problems rather than strategic plans. Although these solutions are, by their nature, highly customised, they may not provide the seamless end-to-end operation or transparency that is essential in modern print shop environments.
In order to pinpoint the areas where money is being left on the shop floor, Solimar Systems offers a walk your workflow service, whereby we work with print shops to examine existing processes and systems and advise on steps to improve them – whether that is installing a Solimar solution or going down another route. While every business and system is different, there are five common problems we encounter time and time again:
· Long time to onboard and process new clients and jobs
· Staff spending too long on repetitive manual processes
· Slow project turn-around times
· System not able to take on new types of work
· Lack of visibility
With the right system in place, these problems can be quickly overcome, delivering a very rapid return-on-investment (ROI). For example, the main areas our customers have seen improvements after the introduction of a Solimar-powered workflow include:
Automation of manual processes – Automating repetitive manual tasks is proven to save companies up to 50 work hours per day. Whats more, it also frees up staff to concentrate on more rewarding and value-added tasks, boosting morale.
The ability to optimize files for production and delivery at higher speeds – Optimized file sizes and structure help print devices run at rated speed and archival storage costs be reduced. Solimar customers have noted that optimized files can be 10 percent or less of the original file size.
Added capabilities to take on additional work types – Compete for more and new types of work with the ability to accept many different print file types with the capability of normalizing them into your standard print and digital delivery processes.
Increased visibility, tracking and reporting – Know what is happening with each job, from onboarding through to delivery, on a secure mobile device, desktop or large format screen view, from anywhere in the world.
Faster project turnaround times – The net result of these efficiencies is the ability to complete jobs more quickly. This was instrumental in helping one Solimar customer, Borns Group, to generate $400,000 of new business in less than a year after installing a Solimar Chemistry PDF-centric workflow management solution.