Offset Printing
Flexible packaging: 80% cost reduction through seamless quality control inspection system
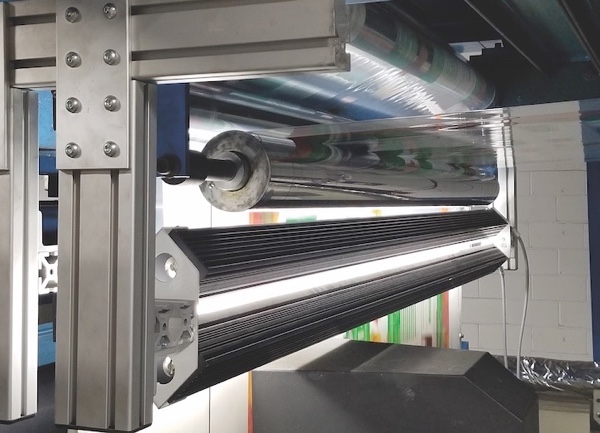
Wednesday 19. May 2021 - To meet the increasing demands of its customers, the US packaging manufacturer Plastic Packaging Technologies relies on the 100% inline inspection system PrintSTAR from the worlds leading supplier of inspection systems ISRA VISION.
More and more brand owners are relying on the powerful impact of flexible packaging to further consolidate their shelf presence in the retail sector. But despite the high demand for innovative packaging solutions, manufacturers are facing tough competition as the demands for high-quality printed products continue to rise.
The experienced team at Plastic Packaging Technologies’ print shop is passionate about producing flexible packaging for food, snacks and pet food, among other products. Despite the many years of experience, there were opportunities to optimise the printing process. In earlier times, highly concentrated operators watched the viewer screen with “eagle eyes” to identify a printing error in time. This process was not seamless because a large number of tasks fell to the operators.
This situation led to a change from “offline” to “inline” for quality control and thus to an automatic 100% inspection system. However, this system not only had to fit the machine exactly, but of course also had to remain within an economically justifiable budget. Other criteria in the selection of the desired inspection system included the possibility to classify defects, as well as a quick set-up and easy operation of the system.
Convincing features of the inspection system
In the search for a suitable inspection system, the company’s attention was quickly drawn to the wide range of products offered by the leading supplier ISRA VISION. Finally, the decision was made in favour of their 100% inline inspection system PrintSTAR. The system, which is used worldwide, offers a complete inspection, even at maximum speed, in order to achieve error-free printing results with absolute reliability. For the press at Plastic Packaging Technologies, a compact two-camera system was implemented that fitted perfectly into the available space. The space-saving system, which nevertheless contains all the technical high-tech features, was precisely tailored to the customer’s needs.
By using high-resolution line scan cameras, in combination with the special and ultra-bright LED lighting, the PrintSTAR system detects and classifies both single and repeated defects in real time. The smart all-in-one camera with embedded colour camera technology combines sensor, processor and interface in a compact and robust housing. The embedded camera’s high resolution of over 8 MPixel and the extremely fast frame rate provide image data with the highest level of detail. The intelligent inspection system not only reliably detects all defects, but also ensures that defined standards and tolerances are adhered to by immediately comparing the print result with the customer PDF. At Plastic Packaging Technologies, the new system detected many register shifts and omissions in particular.
High acceptance for the inspection system
The inspection system could be used in production after only a few days. The acceptance of the machine operators and the production management is immense because it is not only easy to operate, but also ensured maximum productivity in a very short time. By detecting and identifying defects, production, scrap and quality targets can be met better than ever. At the same time, the operator has more time to perform other printing tasks and quality checks because he does not have to constantly watch the screen, as was previously the case. If a relevant defect is detected on the printing foil, the inspection system automatically sounds an alarm.
All detected defects are also logged and classified. The data obtained is incorporated into the analysis of the production process and accordingly improves the workflows and decisions in the print shop.
For the user, the use of the PrintSTAR inspection system has other decisive advantages: The ability to change the accepted defect size in the system allows the operator to better decide when to stop the press to rectify a defect. Unnecessary downtimes in production operations can thus be prevented. The system has also had a direct impact on reducing scrap caused by defects: The yield could be increased because less scrap was now produced.
Reduction of rejects provides cost benefits
The PrintSTAR print inspection system enables different defects to be classified according to size, colour or even defect type, such as stripes, splashes, register errors and colour deviations, precisely in line with customer specifications. For each print job, the customer guidelines and tolerances can thus be determined and limit values entered in a job-specific requirement profile. The operator then receives a display of the errors that exceed the tolerance range according to the specifications and can intervene accordingly in the printing process to avoid waste. Complaints are thus prevented. At Plastic Packaging Technologies, this enormous improvement can be expressed in concrete figures: Between 2019 and 2020, the costs for customer complaints could be reduced by approximately 80 %. In addition to the cost advantage, there is also a gain in reputation with the customer, which is becoming increasingly important in the fierce competition in the printing industry.
Summary
Thanks to the wide range of inspection solutions developed by ISRA, every printing house receives exactly the inspection system it needs. There are no compromises in terms of equipment or quality. Even smaller systems ensure 100% inline inspection with their sophisticated system architecture. Thanks to its user-friendliness and good on-site training, the PrintSTAR inspection system can be seamlessly integrated into production within a few days.
The system’s flexible configuration options ensure the highest possible flexibility in terms of required detection performance for flexible packaging. In addition to the basic configuration for the detection of isolated and repeated print defects, a defect classification system ensures that different defects are classified according to size, colour or even type, precisely in line with customer specifications. Error tolerances and guidelines can thus be determined individually for each print job.
With PrintSTAR, the user benefits from 100% inspected print products and maximum process efficiency. The inspection system also acquires important data for analysing the production process in order to make the best possible decisions. The use of the ISRA inspection system ensures fewer rejects and complaints and thus reduces costs. Lower material usage, quality improvements and time savings ensure a fast ROI of the system. The high reliability to complete even challenging print jobs quickly and without errors strengthens the market position of the printing company and ensures competitiveness even with demanding print jobs.