Offset Printing
Specialist manufacturer CUPSZ chooses Mark Andy Evolution Series E5 – for water-based flexo
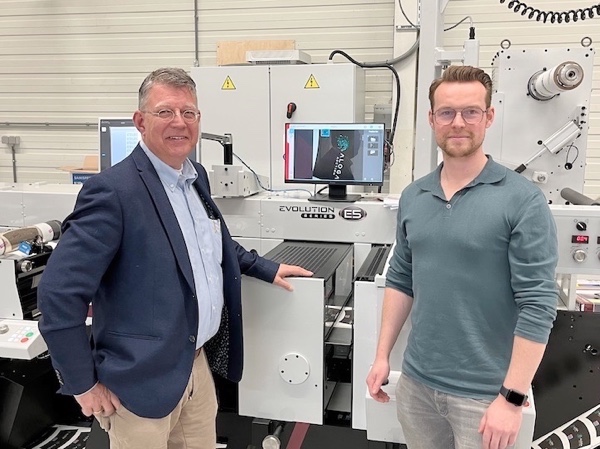
Wednesday 05. April 2023 - Initially outsourcing print, die cutting, and forming production, by 2016 the brothers could see the need to be self-sufficient and embarked on an ambitious plan that in 2019 included securing a 2,000sqm unit on the same industrial park in Tilburg.
The story of CUPSZ began in 2014 when brothers Daan and Michiel Willemsz decided to turn a passion for coffee cups into a profession. Since then, countless coffee cups have been designed and produced at the companys HQ in Tilburg for customers in the Netherlands, Belgium, Germany, and France. Most recently, as part of the companys quest to innovate, CUPSZ has added cardboard disposable containers to its range, known as BOWLSZ.
Initially outsourcing print, die cutting, and forming production, by 2016 the brothers could see the need to be self-sufficient and embarked on an ambitious plan that in 2019 included securing a 2,000sqm unit on the same industrial park in Tilburg. As Michiel quipped: “It was ten times the size we needed for our staff of six, and no sooner had we moved in than the pandemic hit, and the business world looked likely to collapse, and take us with it!”
But, as 2020 wore on, demand began to pick up and with a business model based on high-quality short to medium runs delivered in quick time, CUPSZ was soon busy again. Traditionally, this market was accustomed to a five- or six-week delivery, with the cups coming from Asia. CUPSZ aim was to deliver in two or three days, and in 24 hours if its an emergency, and is currently the only manufacturer in Europe capable of doing this
As the outsourced printing had partly been produced on a toner based digital press, CUPSZ invested in two for the new building and have since built up to a total of seven cup forming machines. “The basic principle here is standardization. We produce only five cup sizes, from 100ml (4oz) to 300ml (12oz), which allows us to dedicate a machine to each size – the time taken to swap tooling would be longer that the total production times on most of our runs, and this way we can guarantee the end-product is leak-free!” he added.
In the customers opinion the digital printing with its relatively slow web speed was always going to be a limiting factor for the business. Runs up to 25,000 cups made sense printed digitally, but larger orders were creating problems and at the larger volumes cost becomes more of an issue. If Covid initially depressed demand it also changed attitudes towards hygiene and single-use disposable paper cups became preferable to china and ceramic that needed washing between uses. By the end of 2020, sales were back to 2019 levels, albeit with lower margins, but the company had survived and was well placed to grow. Throughout 2021 the company celebrated record months, but the brothers knew they were heading for trouble unless they could raise production speeds.
The only narrow web flexo technology that they had experience of was using UV inks and lacquers and CUPSZ was keen to move into water-based technology to maintain an advantage in the market and meet the ever-changing laws on food packaging. The problem was the lack of commercial experience of this with narrow web presses in Europe, but American manufacturer Mark Andy, which largely pioneered water-based flexo in the USA, was able to arrange a full working demonstration of water-based inks in action in the UK. So convincing was the demo, that CUPSZ was left in no doubt that this technology was a viable way forward and ordered a Mark Andy Evolution Series E5.
“What impressed us most was the depth of knowledge and knowhow at Mark Andy. Their water-based presses are not adapted UV lines like the other manufacturers, and this really showed up in the confidence the operators had in changing jobs in five minutes with only 50m of waste. We dont feel weve just bought a press but acquired a partner with fund of useful knowledge to assist us to grow our business,” said Daan.
The new Mark Andy was installed and commissioned in January 2023. Maarten van Bergeijk of Packtion, Mark Andys agent in the Benelux, commented: “Its a 430mm (17″) six-colour Evolution Series E5 with full servo drive, a Vetaphone corona treater and a web cleaner. The six print stations have independent airflow balancing and heating controls and a recirculating dryer base system, and the anilox drive features Oldham couplings and bearings for smooth and accurate operation. Its capable of 230m/min (750ft/min) and is fitted with remote diagnostics and both auto- and pre-register, as well as a BST vision system. There is a servo driven sheeter head and waste windup capable of handling an 810mm reel (32″). As part of the Mark Andy package, we also installed a VPM 400 video plate mounter to ensure accuracy.”
The Evolution Series E5 has a remarkably compact footprint for a press that offers good working space for the operator. “We like the level of automation it has because that makes it easy to set up and run and maintains good quality register – but there is nothing over-complex about it – whats there is for the benefit of the person who is running it, and not a demonstration of how much technology can be added for the sake of it,” said Michiel. The new Mark Andy will be running typically 350 to 460-micron board at around 120m/min, making it significantly more productive than the digital presses at CUPSZ. “Its a very stable press, which is essential when youre running heavier materials, and shows Mark Andys experience with carton board presses – and we cant wait to see how it performs in everyday commercial production,” he concluded.