Finishing & Screen Printing
We have to become faster
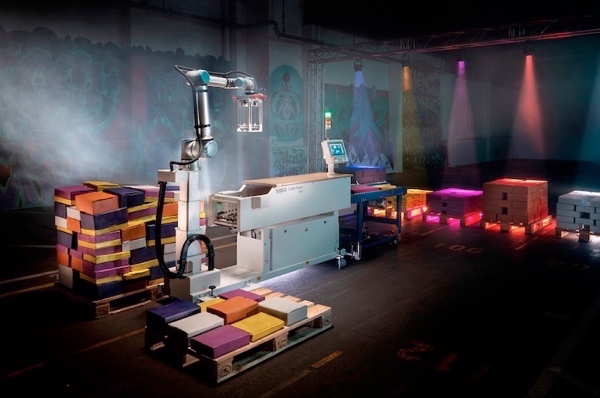
Monday 17. October 2022 - With the team at MBO Postpress Solutions GmbH, Managing Director Thomas Heininger is looking for efficiency potential on all fronts. The company from Oppenweiler is taking unconventional - but successful - paths towards the goal of climate neutrality.
In the “Circular Competence” interview series, the VDMA Printing and Paper Technology Association asks its member companies about their plans, solutions, and challenges on the road to a circular economy. What can the industry do to minimise the ecological footprint of packaging and other printed products?
With the team at MBO Postpress Solutions GmbH, Managing Director Thomas Heininger is looking for efficiency potential on all fronts. The company from Oppenweiler is taking unconventional – but successful – paths towards the goal of climate neutrality.
By the middle of the century, the leading industrial nations want to have a climate-neutral economy. Is this goal realistic in your view?
I am convinced of that. We should even do it much sooner. Because we see the consequences of climate change everywhere. My family had a ski lift near Munich. I learned to ski there as a child. This lift could no longer be operated because it hardly snows at medium altitudes. And in the summer, we had no school attendance at 27 °C. Today’s children would hardly still be in school. The changes are drastic and threaten the existence of many people. The costs of climate change increase the later and slower we act. Or metaphorically speaking: We are sitting on a powder keg and the fuse is very short.
What are you doing to minimise the energy demand of your production?
It starts in small ways: We finance our employees’ bicycle leasing and annual tickets for public transport. We operate a growing fleet of electric cars and hybrids as company cars, we have LED lighting everywhere and we consistently invest in photovoltaics. It covers two thirds of our electricity needs. In Portugal, we are building another plant with a peak output of 700 kilowatts. And this will not be the last. Because at current energy prices, a PV system pays for itself in less than two years. But that’s not what matters to us. First and foremost, we want to be fit for the future. This can only be achieved if we adapt to change. This reaches deep into our corporate culture. We encourage our employees to continue it at home. If they charge their company cars at their own solar system, we pay for it. Our trainees independently planned and realised a covered charging station for eBikes in a project. They won prizes for it at the state level, and we market their solution in the region. When I started here, the company had no apprentices. Now there are 15 to 17 in total every year, partly because word gets around that they learn in meaningful projects with us. We are also currently planning and examining a four-day week. I am convinced that it is good for our employees to recharge regularly and then get more done with fresh energy. Of course, one more day off also reduces our energy needs.
How do you support your customers in producing more energy efficiently?
With around 400 employees, we are a small medium-sized company specialising in finishing solutions. The potential for savings is limited, as are our human resources. One of the ways we solve this is by assigning master’s theses to mechanical engineering students. In one of these projects, a student systematically worked on optimising the air flows in one of our folding machines. By using a more efficient pump, an improved control system and simulation-based optimisation of the air flow and nozzles, which we subsequently manufactured additively, the energy requirement of this machine is significantly lower. The master’s thesis was a 1.0 and of course we hired the student directly. Projects like this, which don’t end up in a drawer but lead to sustainable improvement, are a way of not only finding skilled workers but also retaining them. That’s what it’s all about. Demographic change is underway. In ten years, the German economy will lack seven million workers. But back to energy efficiency. Often it runs almost unnoticed, for example when it is primarily a matter of eliminating inhuman monotonous manual labour and increasing productivity. We have a largely autonomous 4.0 chain in which an autopilot is integrated that supports production planning and enables automated signature changes, a camera-supported fold quality control ejects misfolded sheets and a cobot stacks the folded sheets ( www.cobo-stack.com). At the same time, energy consumption is reduced in a steady production process that runs smoothly despite frequent job changes. This is because machines consume an unnecessarily large amount of power when idling or constantly starting up.
What role does the topic play in your research and development?
It’s about the question of whether we should optimise technology, which in principle has hardly changed for decades, in small steps as before – or throw all that overboard and think completely anew. That is what we are dealing with. What does a folding machine look like that is realised with the most modern development and production methods – and in which productivity and energy efficiency are in the foreground from the first stroke of the design drawing. I am convinced that as a company we can improve on all fronts – and must always be prepared to rethink our processes and our products. Buildings, heating, and cooling are as much a part of this as our own power generation and mobility. Everything is connected. We are challenged as a society and as a company to think and implement change holistically. To this end, we also invite experts from different fields to get to know new points of view, to rub up against them and to be inspired.
What would you like to see from legislators on the road to climate neutrality?
I would like to see investments in climate and environmental protection written off more quickly. Because I think that would speed up many decision-making processes – and as we said at the beginning, we have to become faster. I would also like to see legislators setting the framework conditions more consistently so that innovations find their way into the market more quickly. Lax regulation has the effect that cheaper, usually more inefficient technology is bought. As a country that exports key technologies of the future all over the world, we have to stay ahead of the game. Strict regulation forces industry to innovate, which then finds markets worldwide.