Finishing & Screen Printing
“Automation only makes Sense where it pays off”
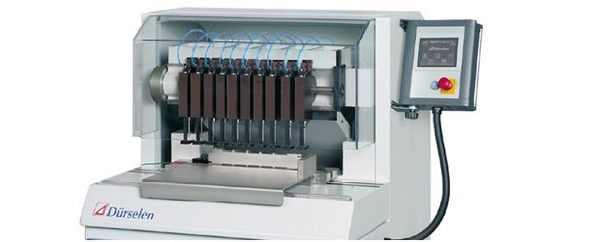
Friday 25. November 2016 - Mönchengladbach-based Dürselen GmbH & Co.KG is leading in the paper drilling technology sector. Besides that, it develops and manufactures special machines and automation solutions. Interview with Dirk Berg, Executive Partner.
Mr. Berg, could you please give a brief introduction about your company Dürselen?
Dirk Berg: Yes, certainly. After its establishment in 1966, the company has grown from being a supplier of components to a machine building company – and already specialized in paper drilling machines and peripheral equipment in the 1990s. Furthermore, we offer transport and packaging systems as well as the built-to-order production of large-dimension components and precision parts. Additionally, we develop and build special machines, including automation solutions. At present, we have 22 employees, among them three trainees. Our annual sales are about 2.5 million Euro. I took over the company and its management in autumn 2015 from the previous owner, Hans-Joachim Dürselen, who wished to leave because of his age.
How does the breakdown of your sales as regards these sectors look like?
Berg: Paper drilling technology, finishing systems and packaging machines for the graphic arts industry account for approximately one fourth of our total sales. The other 75 per cent are spread among production services and our work as a supplier. We mill and drill precision components and large-dimension parts with up to 16 metres in length and a weight of 50 tons. Our customers are machine tool engineering companies, textile and packaging machine manufacturers, suppliers to the automotive industry and companies of the aircraft and aerospace industry.
Who are your customers in the graphic arts industry?
Berg: They are mostly the end customers – i.e., bookbinding companies and printing houses. We have a global network of authorized dealers who sell our machines and in most cases also provide customer services.
To what extent do you see digital processes in “paperless offices” as a threat to your paper drilling technology?
Berg: I don’t see digitization as a threat. It’s a challenge of the future that we accept. It is obvious that the number of units as regards paper drilling machines is decreasing and will not return to the level of the last few decades. We devote much energy on holding our leading position in the increasingly shrinking market – and on strengthening it.
How?
Berg: By continuously improving our machines and by adding new technical features. In qualitative terms, we already lead the field. We receive orders for a general overhaul of machines that have been operated by our customers for much more than 20 years, and they will then run smoothly for at least ten more years. Of course, we would prefer selling new machines – but this quality speaks for our brand.
At drupa 2016, Print 4.0 with digitally networked process chains was one of the dominant themes. Is it to be expected that networked paper drilling technology will accompany digitization with its rising sales figures?
Berg: Of course, there are printing houses that pursue this path towards Print 4.0. There are, however, also many small bookbinding companies and backyard print shops that are unable to manage these investments. Furthermore, the digital printing houses need not replace the paper drilling equipment they already have just in order to integrate newly purchased technology into 4.0 process chains. Our machines have the necessary interfaces for integration into the networked production process.
You offer office paper drilling machines with one to two drill heads, but also programmable paper drilling machines with 22 drill heads. In which respect are drills better than die cutters or lasers?
Berg: When you drill, you get burr-free holes. The paper is not damaged and can, therefore, be processed in a better way. In addition, the combination of different hole solutions is easier. Take, for instance, the calendar where you need holes for the wire comb binding and an additional thumbhole in the middle.
Your systems are designed to ensure minimum wear – drill belts as drilling supports, adjustment of reground and new drills in µm-precision, cooling and lubrication within the process
Berg:
with the dosage of lubrication and cooling being so fine that it leaves no visible traces on the paper. With that and the other measures already mentioned, we ensure considerably longer service lives of the drills. In order to increase the productivity even further and to reduce the set-up times to a minimum, we are also working on the combination of different operational steps. The aim is to reduce the cost per item by means of more efficient process solutions.
In the set-up operations of your machines for varying hole distances, the drill heads are still moved manually. Are there any automation approaches in this respect?
Berg: Yes, for that we have developed our DOD (drilling-on-demand) models. These machines can produce all kinds of drill patterns and arrangements from batch size 1 fully automatically in a networked process. Nevertheless, the manual adjustment is more cost favourable and therefore more efficient with higher batch sizes.
One question as to your engineering activities. Do you see additive manufacturing methods as a possible supplement for the manufacture of precision parts or single components for special machines?
Berg: We are keeping an eye on that technology. I could definitely imagine that we will make future investments in that technology – if this pays off for us in economic terms.
Do you have plans for further internationalization and sector diversification?
Berg: We will not start manufacturing activities and establish our own representations abroad – but rather extend our network of authorized dealers. As to diversification: We are working on transferring our know-how to other fields like the packaging sector. One example is our Dürselen VA 02 automated stack packing system that packages brochures fully automatically. No doubt, the packaging market is interesting. However, our know-how is also useful in special machinery engineering and automation solutions which we implement for our customers.
When you think of Dürselen in 2030, which vision do you have?
Berg: We will be a brand that stands for top quality, both in the graphic arts sector and in manufacturing services. Over the lasts 50 years, Dürselen has made an excellent name for itself, which we wish to maintain. Whoever needs paper drills, precision parts or automated special solutions will get profoundly solid and well-planned solutions from us in the year 2030 as well.