Consumables
When the sustainability of packaging begins with the flexographic printing plate
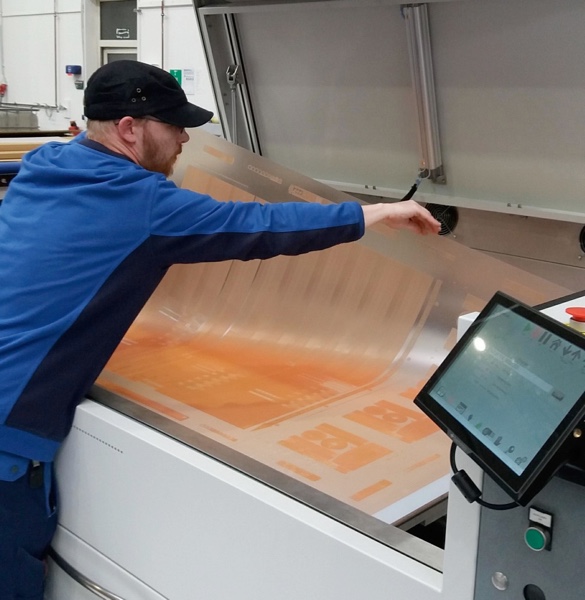
Tuesday 29. October 2019 - U. Günther GmbH enables more business and brand owners to round out their sustainability strategy with innovative, sustainably manufactured KODAK FLEXCEL NX Ultra Plate Packaging Printers
Sustainability is one of the current megatrends in the packaging market. Ecologically advantageous packaging is increasingly in demand from brand owners and retailers. The U. Günther GmbH is expanding its printing plate portfolio with new high-quality plates for packaging flexo printing, which combine sustainability and efficiency in production with high printing quality and optimum printing properties. The packaging prepress service provider, headquartered in Hamburg and with printing form production in Greven, Mecklenburg-Vorpommern, is one of three beta test users of the KODAK FLEXCEL NX Ultra solution in Europe. This innovation from Miraclon – formerly Kodak’s Flexographic Packaging Division – offers all the unique technology advantages of KODAK’s established FLEXCEL solutions, but works with solvent- and VOC-free, water-based processing. In addition to this ecological advantage, there is a speed advantage: a print-ready, high-quality flexo plate can be produced in less than an hour.
In February 2019, the FLEXCEL NX Ultra solution was introduced by U. Günther. As the company has been using KODAK FLEXCEL NX systems since 2013, they were already familiar with the technology. Only the new FLEXCEL NX Ultra 35 processing system, which uses KODAK’s patented Ultra Clean technology, needed to be installed.
“The demand from brand owners and private label companies for environmentally friendly packaging solutions is growing. This means that packaging printers are facing new challenges, for which we can offer adequate support in the area of printing formes with FLEXCEL NX Ultra. This means that the sustainability of modern packaging starts with the flexo plate,” says Stefan Schneider, Sales Coordinator at U. Günther. “In addition, FLEXCEL NX Ultra clichés offer packaging printers a range of handling, quality and productivity benefits. They are very easy to integrate into print production. Current tests and first productions show us that the plates deliver excellent print quality with high edge sharpness and first-class highlights. The plates remain open longer during printing, so printers benefit from longer cleaning intervals and thus less machine downtime. In addition, the printing speed can be significantly increased.”
Packaging manufacturer scores with customers for environmental benefits of FLEXCEL NX Ultra plates
No wonder, then, that the sales specialists at U. Günther are happy to recommend the new FLEXCEL NX Ultra sheets to customers. LPF Flexible Packaging, a Dutch manufacturer of flexible packaging and part of the international Clondalkin Group, has long purchased flexographic printing plates from U. Günther. “When customers ask us about progress in the sustainability of our packaging, we always refer to the possibility of using the new solvent-free printing form to extend the sustainability of the packaging to the pre-print area,” explains Henk Edzes, Sales Manager at LPF Flexible Packaging.
In the meantime, LPF’s first production runs with FLEXCEL NX Ultra plates in film printing for sustainability-conscious customers in the confectionery sector have started – with excellent quality results. Production volumes ranged between 15,000 and 50,000 running metres. “Our printers are enthusiastic about the plates. They no longer smell of solvents when unpacked, are easier to assemble and do not set up as quickly during print production,” says Henk Edzes about LPF’s experience. “They also need to wash the clichés less frequently and can increase the printing speed, which improves our productivity.
FLEXCEL NX Ultra Solution for More Efficiency and Better Service
At U. Günther, the FLEXCEL NX Ultra solution has become an integral part of the flexo portfolio after only a few months. “The qualitative properties are absolutely convincing and the short process time enables a significantly higher plate throughput,” confirms Thomas Pyssa, Production Manager at U. Günther. “In addition, FLEXCEL NX Ultra requires less maintenance than other water-washable and solvent systems”.
The use of the new technology at U. Günther obviously has a win-win effect for everyone involved: for packaging printers, for their customers in the branded goods, private label and retail sectors and for the prepress service provider itself.