Offset Printing
Customers Throughout Europe Secure a Competitive Edge with the Speedmaster XL 105 with Perfecting Device
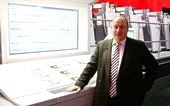
Tuesday 12. May 2009 - Industrialized production with enhanced productivity and quality thanks to Prinect Inpress Control inline measurement; British magazine printer orders second long perfector with CutStar sheeter; Packaging and commercial print shop in Austria uses FoilStar cold foil module for inline finishing; Major Swiss printing group invests in alcohol-free printing
To hold their own on a competitive market, industrial print shops are having to meet an ever longer list of requirements from customers, including fast delivery times, shorter run lengths, high quality, and exquisitely finished end products. Customers who use the Speedmaster XL 105 with perfecting device to keep their pressrooms up-to-date clearly have the edge in this regard. This Peak Performance Class press, which Heidelberger Druckmaschinen AG (Heidelberg) unveiled with perfecting device at drupa 2008, is becoming a benchmark in the 70 x 100 centimeter (27.56 x 39.37 inch) format thanks to its range of automation components. The modular platform plays a key role in this. For example, one of the options available is the Prinect Inpress Control spectrophotometric inline measuring system. This module automatically measures and controls color and register in the press and forwards any necessary corrections directly to the Prinect Press Center control station. Process colors, spot colors and register in the quality control strip are factored into the calculation.
DetailsBritish magazine printers already using second long perfector with CutStar sheeter
British printing group Stephens & George, near Cardiff, recently began production with its second long perfector, a Speedmaster XL 105 ten-color press with Prinect Inpress Control and CutStar. The pressroom already houses a Speedmaster XL 105 eight-color press, also with CutStar. Stephens & George uses the two presses primarily to print magazines, thus providing backup for its Speedmaster SM 102-12 P. “Both presses are fitted with Prinect Inpress Control and we are very impressed with the speed of makeready and the way it gets to top quality quickly and retains it throughout the run,” says Group Managing Director Andrew Jones. “The XL 105 really does run continuously at a speed of 15,000 sheets per hour and with CutStar provides a really industrialized solution,” adds Jones.
The Company says the Speedmaster XL 105 is achieving at least 30 percent better productivity than the Speemdater SM 102 series presses and, at the end of last year, the eight-color Speedmaster XL 105 topped the five million impressions a month mark.
“The problem remains that the industry is still cutting prices so we are running faster to stand still. You have to have the right technology to remain in the game. Our turnover last year was £20 million and we have budgeted for a slight increase in the current financial year,” says Jones.
Website: www.stephensandgeorge.co.uk
DetailsPackaging and commercial print shop in Austria uses FoilStar cold foil module for inline finishing
The same confidence is shown by Sandler Print & More & Co KG in Marbach, Austria. This print shop employs a workforce of 25 and in the last two years alone has invested five million Euro in a Speedmaster XL 105 six-color press, elevated, with coating unit and material logistics, which mainly prints packaging. This was quickly followed by installation of the Speedmaster XL 105 eight-color perfecting press, equipped with coating unit, CutStar sheeter, FoilStar module for cold foil finishing, and corresponding paper logistics.
Both presses replace products from another manufacturer. This move was preceded by an intensive period in which tenders were invited and practical tests conducted. “We saw in practice that the productivity of the Speedmaster XL 105 is 30-40 percent higher than for presses of the previous generation,” says Managing Director Hannes Sandler, summarizing his decision.
As well as the technical benefits, Heidelberg also won the company over with the Systemservice 36plus concept. “We arent just buying presses – we are also buying the security of knowing that the presses will deliver unlimited availability for our customers orders,” adds Sandler. The CutStar sheeter and Prinect Inpress Control inline measuring unit are a response to the tight margins in commercial printing. “We produce long runs and here we can fully utilize the potential of a perfecting press with XL technology combined with CutStar. XL technology enables us once again to achieve the margins that you need to survive in the print industry.”
The press runs at a constant 15,000 sheets per hour in tandem with the perfecting device and CutStar. Although the difference in price between sheet stock and reel paper is not particularly great, Sandlers CutStar pays for itself through the consistently high production speed and optimized warehousing.
Finishing continues to grow in importance in both packaging and commercial printing. For instance, metallic effects can be produced inline and efficiently on the Speedmaster XL 105 using the FoilStar module for cold foil finishing. Overprinting foils makes for truly eye-catching features at the point of sale. The FoilStar module has been installed on the eight-color press, enabling cold foils to be overprinted with up to six colors at Sandler, which is an absolute first in Austria. “This eight-color press therefore allows us to serve both the high-quality market and the high-volume commercial market.” Using Prinect Inpress Control boosts productivity and ensures a high level of quality for both presses.
This application has also been certified at the Sandler print shop by FOGRA to ISO 12647-2. Both Speedmaster XL 105 presses are integrated into Sandlers management and production workflow. The Prinect Prinance management information system (MIS) and the Prinect Printready workflow are key components in this process, ensuring a smooth exchange of information between administration and production. The next stage in the networking process involves the installation of Prinect Pressroom Manager with the “Scheduler” option – the electronic planning board in the Prinect workflow.
Today, two Speedmaster XL 105 presses can produce the print volume that previously required three presses. “While other print shops print 25 million sheets a year with their perfecting presses running in three-shift operation, we produce this volume in one to two shifts. In three-shift operation, it would be possible to print over 60 million sheets a year,” says Sandler confidently.
Website: www.sandler.at
DetailsMajor Swiss printing group to print without alcohol in the future
PMC Print Media Corporation, based in Oetwil am See in Switzerland, has ordered a Speedmaster XL 105-5-P+LX3 and hopes for similar effects. This five-color press with coating unit and DryStar dryer systems in the triple extended delivery will replace two presses from another manufacturer in August this year.
By investing in cutting-edge sheetfed offset technology, the company is looking to pursue growth, with complete updating of the pressroom equipment being essential to achieve its qualitative and quantitative targets. As well as sheetfed offset, PMC Print Media Corporation also uses a 16-page web offset press with five double printing units in two to three-shift operation.
The decision to invest was preceded by an extensive selection process. “We drafted a comprehensive wish list covering technology, service and price/performance, thereby creating the basis for an objective and fair assessment,” explains Managing Director Erwin Lüber. “The Speedmaster XL 105 performed best in the overall assessment and our own calculations were confirmed by Heidelberg Business Consulting,” added Lüber. For him, the scope of the offering, together with the three-year Systemservice 36plus warranty and service package, was a crucial factor.
The Speedmaster XL 105 ordered is perfectly equipped for the task ahead. Key features include adjustment of register and ink feed in the inline process using Prinect Inpress Control and simultaneous plate changing with Autoplate XL. The printing system is operated from the Prinect Press Center control station, which displays the press functions and production status on the large wallscreen. The new CombiStar 3000 Pro is used for inking unit temperature control and preparing the dampening solution. The aim is to use the two-stage dampening solution filtration (beta.f filter) for alcohol-free production in the future, thus protecting both employees health and the environment.
PMC Print Media Corporation is part of WRH Walter Reist Holding AG, which also owns Ferag AG, a leading global supplier of systems for industrial finishing. The PMC production facility in Oetwil am See is also the alpha test center for new Ferag developments and an internationally renowned showcase for cutting-edge technology in press and postpress.