Packaging
Hapa Extends Late Stage Customisation Capabilities With Range Additions
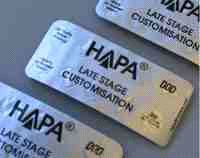
Wednesday 30. April 2008 - Following last years launch of the 807 BlisterJet UV Drop On Demand inkjet system, Hapa has announced a significant strengthening of its 800 range with the launch at interpack of two new models - the CartonJet and LabelJet - enabling pharmaceutical manufacturers to benefit from greater flexibility and productivity, as well as improved Overall Equipment Effectiveness across their packaging operations.
The CartonJet handles pre-folded and glued cartons, while the LabelJet is available in reel-to-reel or inline executions. Each standard system is a complete unit incorporating printer modules combined with a customised product handling and transport system, offering a full digital four colour (CMYK) approach. The LabelJet includes the intelligence to complete the current print cycle during line stoppages, thereby ensuring that there is no impact on print quality or packaging line efficiency.
The Hapa 800 series is built around UV Drop On Demand, digital printing technology. This produces extremely high quality print thanks to sophisticated drop placement, with the capacity to print at full blister, carton or label web width. The printheads operate with high specification UV inks, which are extremely resistant to both smudging and scuffing.
Handling systems are designed to accommodate different sizes of carton or label web widths respectively and to ensure accurate printing. To comply with pharmaceutical quality and good manufacturing practice requirements, inspection systems are integrated at the infeed and outfeed to verify that the correct information has been applied to the correct product. Items failing either quality check are diverted into a secure eject station.
Print data from standard artwork packages can be uploaded to the printer by means of a secure digital interface and the system is fully compliant with the FDAs 21 CFR part 11 regulations. The increasing demand for sequential numbering and unit dose coding are also catered for thanks to the fully-digital system concept. At the same time, the ability to print both artwork and variable data in a single pass brings high flexibility to production planning.
Sales Director at Hapa AG, Tibor Gal, explains that the Hapa 800 series is the ideal Late Stage Customisation solution for pharmaceutical manufacturers facing the most extreme demands on their production. “Variations in product, dosage strength, pack sizes and local market requirements traditionally create the need for hundreds of different packaging variants,” he says. “With in-house late stage customisation, however, the need for huge inventory is largely alleviated: instead, companies can use blank or part-printed stock which, for the handling of complex production schedules with many short batches, delivers a host of benefits.”
These include easier and less costly stockholding, elimination of obsolete packaging stock resulting in significantly reduced waste, and the ability to save through bulk purchasing of blank materials. In addition, changeover operations on packaging lines become markedly more simple, as in many cases the same blank or generic stock can be used from one batch to the next, radically reducing the complexity of line clearance and reconciliation procedures.
“Late Stage Customisation with the Hapa 800 enables pharma producers to satisfy customer demand almost immediately, thereby meeting the twin objectives of increasing customer satisfaction through reduced lead times, while improving operational efficiency and profitability,” concludes Tibor Gal.