Offset Printing
Hornslet Bogtrykkeri orders KBA Colora
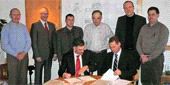
Monday 28. April 2008 - Denmark: new newspaper technology to drive growth
Danish printer Hornslet Bogtrykkeri in Hornslet is celebrating its centenary by expanding production capacity with a KBA Colora. Signed in mid-April, the contract is for a 4/2 press line that will be installed alongside an existing 2/1 press next year. Hornslet’s location some 20km (12½m) north of Aarhus is ideal for distribution throughout East Jutland.
Says managing director Hother Hennings: “We are adding a second press line in order to address a need for shorter production times and more capacity with a high print quality. The Colora will not only expand capacity but will also furnish much greater flexibility because we’ll be able to print low- and high-circulation titles simultaneously and thus more efficiently. The contract for the four-across Colora was the culmination of an exhaustive selection procedure which took us to a number of two-across and four-across reference installations. What settled the issue was the Colora’s high output, excellent print quality and sheer value for money. Its cutting-edge technology will enable us to enhance our competitiveness by offering a product spectrum ranging from 5,000 8pp copies to literally millions of high-pagination copies.”
Flexible technology for up to 64 tabloid pages
The 75,000cph floor-mounted press has a cylinder circumference of 1,120mm (44in) and can handle a maximum web width of 1,590mm (62½in). It will be configured with two KBA Pastomat C reelstands fed by a KBA Patras A automatic reel-handling system with stripping station. The two four-high towers will have automatic ink pumping, colour-register control and fan-out compensation. Further the press comprises two turner bars, a folder superstructure with two formers, a KF 3 jaw folder with a 2:3:3 cylinder ratio, a section and ribbon stitcher and a quarterfold capability. Provision has been made for the addition of a skip slitter, a gluing unit and length/cross perforators at a later date. The advanced level of automation extends to the control technology and will include job preparation and press presetting, a RIP interface to CTP pre-press for presetting the ink keys, and a diagnostic PC for remote maintenance.