Offset Printing
KBA – the no 1 in packaging presses
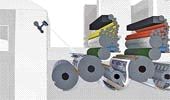
Thursday 17. April 2008 - Why choose a Rapida?
For many years now KBA has been the leading provider of sheetfed offset technology to the highly automated packaging sector. This is not limited to large format: fully 50% of the Rapida 105 and 105 universal medium-format presses that leave the production line at its Radebeul facility are destined for packaging or folding carton production.
The reasons for this well entrenched market position are manifold, ranging from the wide range of substrates the Rapidas are capable of handling, to KBA’s formidable know-how in coating (a process dear to packaging printers’ hearts) and process innovation, the quality and durability of its presses and the customised configurations it can offer complete with integrated substrate logistics.
In the print media market, packaging often represents the crowning touch in enhancing a product’s visual impact and appeal at the point of sale. Packaging should be striking, easily noted and recognised and yet cheap to produce. So Rapida presses, from half-size to the superlarge 205, are the ideal choice.
The original comes from Saxony
Smooth sheet travel entailing minimum curvature is crucial when printing heavy board, corrugated or thick plastic sheets. And it is no coincidence that this concept was first realised in Radebeul back in 1965 with the development of double-size impression and transfer cylinders and the unit-type press design. It allows medium- and large-format presses to print board up to 1.2mm (48pt) thick and microflute with a maximum calliper of 1.6mm (0.06in). With the appropriate modifications they can handle even thicker substrates such as beer mats. Since then all press manufacturers of note have adopted the machine design pioneered in Saxony, but generally tend to regard packaging presses as a sideline, whereas for KBA in Radebeul they have been a primary market for many decades.
However, the basic concept of a press is not everything. It must be enriched with features that will deliver a high output, support a range of finishing options, encompass substrate logistics and include total quality control. Here, too, KBA has a lot to offer.
The many facets of inline finishing
Presses with one or more coating units have become a standard feature in packaging printing. Whether aqueous or UV coatings, solid, blank or spot coatings – anything is possible with anilox coaters. KBA has developed and perfected new technologies such as hybrid printing and coating, which can create some fascinating matt/gloss effects.
Nowadays, changing the coating and cleaning the coater are no longer the time-consuming tasks they used to be. The same applies to changing the coating formes or the doctor blade. Changing the coating plates on Rapida presses – both medium and large format – has long been automated, but without this fact being trumpeted as a world first. So conversion is no longer as laborious as it was just a few years ago. The volume of coating applied, and the quality of the coating, can be controlled precisely by using different anilox rollers (cf KBA Process 4, pp 28-31).
Well ahead in green printing
Rapida presses attained “emission tested” accreditation in 2000 and since then have been awarded eco-certification that is recognised by the competent authorities in numerous countries. This applies to print production on both paper and board with conventional, hybrid and UV inks, and aqueous and UV coatings. Low-alcohol or alcohol-free production is also used on a daily basis in many printing plants, even for highly challenging applications. When it comes to environmentally responsible print production, KBA has long been the acknowledged mover and shaker, just as it is in inline coating.
Marketing alone is not enough
Rapida presses can do more than coat: with the appropriate kit they can also cut, perforate, number and even die-cut. A corona discharge unit is available for treating synthetic materials prior to printing, while KBA ColdFoiler takes the witchcraft out of cold-foil stamping. This is particularly useful for products where metallic coatings would not deliver the standard of quality specified. And the first open house in Germany – and indeed in Europe – on the subject of brand protection took place in November 2004 at KBA in Radebeul, where live demonstrations were given on Rapida presses. As with many other technologies, its competitors did not jump on this particular bandwagon until very much later. In packaging printing, marketing alone is not enough: success depends on recognising and actively shaping emerging trends. KBA has consistently remained at the bleeding edge of technology.
Printing thick, rigid substrates presents a real challenge both to the press and its operators. Here, too, KBA offers a string of specialist aids. For instance, in place of the manual nonstop feeder its Rapida presses can be configured with an automatic version. This comprises a rake which is located beneath the suction-tape feed table and automatically inserted between the residual pile and the pallet. It then raises the residual pile so that the pile change can be completed without undue haste, even when thick, heavy substrates are being printed. What is more, the feeder can still be accessed from all three sides.
A fundamental advantage of the height-adjustable nonstop roller in the delivery is that it is inserted in the direction of sheet travel and therefore functions much more reliably and with far fewer missing-sheet stoppages than other systems. The ability to lower the pile means that there is more time for the pile change. Both automation modules develop their full potential when they are used in conjunction with an automated pile logistics system. Various logistics components can be networked to form a customised, application-specific holistic concept that can embrace pallet-free transport systems and the logistics systems at the feeders and deliveries of several presses.
New products at Drupa
One new product that KBA will be launching at Drupa is PileTronic RFID, the initial component in an RFID-monitored substrate logistics system entailing the detection and identification of numbers attached to the pallets in the feeder and delivery. A read/write device installed at the feeder reads the job-specific ID number stored on a chip in the pallet and presents it via LogoTronic Professional to the MIS/PPS for cost accounting, scheduling and logistics purposes. KBA PileTronic RFID can also be used to locate all the pallets in the production hall.
In packaging printing it is vital that the image of the branded goods packaged should in no way be impaired by colour fluctuations, misregistration, tinting, ghosting or hickeys. The print quality must therefore meet the very highest standards. So end-to-end quality monitoring and control, complete with the appropriate documentation, is absolutely essential. This has been available from KBA for many years in the form of its QualiTronic inline sheet inspection system.
With QualiTronic, which was originally developed for security presses, the sheets can be inspected throughout the entire production sequence, ensuring 100 per cent control. At Drupa KBA will be showing two spectacular new features for this system. One is an inline colour measurement and control system that scans the measuring points on each sheet, records differences in density and automatically makes the adjustments necessary to obtain the correct density. For greater convenience the current density values are displayed in real time at the console, so there is no need to extract a sheet from the press for measurement. In the process a comprehensive quality protocol is generated on all the measured values in the job, providing hardcopy evidence of quality throughout the entire production chain. KBA’s development engineers are also busy devising new ways of detecting and ejecting faulty sheets and, in due course, faulty blanks. Some of these will be demonstrated at Drupa.
The other new feature is DensiTronic PDF, which is embedded in the DensiTronic desk. DensiTronic PDF scans the entire sheet and compares it with the approved original PDF.
Decades of close and successful collaboration with international packaging enterprises have resulted in KBA becoming the acknowledged market leader in sheetfed offset technology for printing packaging. And there are a lot more interesting developments in the pipeline for enhancing quality and efficiency and creating fresh applications, not least for brand protection, an issue of emerging importance in the industry. So the packaging industry will continue to enjoy KBA’s support as a dedicated and competent partner.