Offset Printing
Value added with environmental accreditation
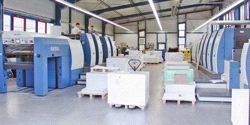
Thursday 27. March 2008 - Stieber Druck in Lauda-Königshofen
German print provider Stieber Druck in Lauda-Königshofen combines production to industrial standards with a commitment to environmental conservation. This is evidenced by accreditation to PEFC, FSC and ISO 14001 standards. In conjunction with ClimatePartner this mid-cap enterprise also actively pursues carbon-neutral media production. The fact that such a commitment delivers economic benefits is a welcome extra.
An all-inclusive print provider with around 120 employees, Stieber specialises in commercial, sheetfed and digital print production while offering a complete range of pre-press, post-press and mailing services. An in-house media agency even handles programming services, for example for internet applications.
Compliance with DIN 12647/2 (Process Standard for Offset) and with ISO 9001 (quality management) guarantees a predictable and reliably reproducible print quality, which is the company’s prime focus.
Stieber’s approach to conservation is equally wholehearted. FSC and PEFC accreditation guarantees that only paper from renewable sources is used, and proof can be provided if the customer wishes. The conditions for PEFC certification are not quite as rigorous as for FSC, and enable smaller forestry enterprises to document their participation in environmental schemes.
ISO 14001 accreditation commits a company to ongoing improvements in environmental efficiency throughout its production chain via a sophisticated environmental management programme based on planning, implementing, monitoring and optimising an operational environmental policy and environmental objectives. Compliance is monitored and regularly audited by external auditors. Accreditation is more than just a declaration of intent – it symbolises provable, practical achievements.
Stieber’s environmental policy embraces new technologies for conserving resources. In December last year the company pressed the button on a KBA Rapida 105 with DriveTronic semi-automated plate changing, installed alongside two existing presses of the same type. With run lengths steadily diminishing and the number of print jobs steadily rising, the new press, which incorporates dedicated drives for the plate cylinders, affords huge potential for cutting makeready times and material consumption, thus enabling Stieber to reduce its ecological footprint while boosting revenue.
On average the new four-colour press cuts a full five minutes off each makeready. With 30 job changes per day in two shifts, the total daily saving is 150 minutes. But this is only possible if jobs are well prepared. Plates and paper must be ready at the press, and the operator needs a helper if he is to exploit the productivity potential to the full. Savings in material consumption are also substantial over a period of time. Management is confident that the additional outlay for DriveTronic SPC will be recouped before the end of the year.
Carbon-neutral media production
The principles of carbon-neutral media production are based on the voluntary emissions trading laid down in the Kyoto protocol. This decrees that the location of CO2 emissions and reductions is irrelevant because greenhouse gases disperse evenly throughout the atmosphere. Emissions from one location can therefore be offset by savings on a similar scale at a different location. Replacing a diesel generator in an Indian village with a biogas plant offsets the equivalent volume of CO2 emissions elsewhere.
Stieber opted for accreditation through ClimatePartner because this is achieved by sponsoring projects in developing countries that deliver a sustainable benefit to the local population along with the reduction in emissions. Such projects could not be implemented without the financial input of emissions-trading mechanisms.
The first step in qualifying for a “carbon-neutral” label was to measure precisely the total power consumption of all machinery and equipment, not forgetting heating and air-conditioning systems. Even the average commuting distance for employees was included in the calculations. Stieber was more than happy to leave this to ClimatePartner, which had already built up a vast database on CO2 emissions from papermaking, to which the company data could then be added. The result was a reliable calculation of total CO2 emissions from felling the trees for the paper to delivering the finished prints to customers. ClimatePartner used the data generated to devise a carbon calculator that could be used to work out the carbon emissions for each individual print job.
Doing well by doing good
Quite apart from the satisfaction gained in making a valuable contribution to the fight against global warming, the effort expended in conserving the environment can deliver material day-to-day benefits for mid-cap enterprises like Stieber. Not only is it possible to achieve a substantial saving in running costs, but a new product is created in the process that can be marketed accordingly. Stieber’s commitment to conservation has gained it new customers, helped to retain existing ones and given sales a big boost.
Customers profit just as much as Stieber does from its positive image and accredited input in aid of climate protection. And at very little extra outlay: around 1% of the total job cost.
Well equipped
Stieber’s example clearly shows that with farsighted management, modern production tools and standards and a willingness to innovate it is possible to combine an environmental conscience with higher earnings.