Finishing & Screen Printing
Tru-Vision Plastics finds clearer future with Colter & Peterson SABER cutting system
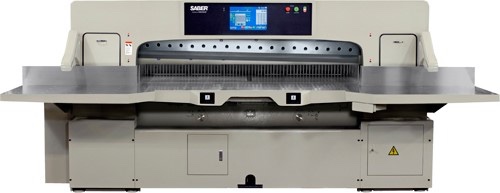
Thursday 20. October 2016 - Cutting squares and rectangles isnt limited to just paper. Ask Ted Dean, President and CEO of Tru-Vision Plastics in Brenham Texas. Needing a better solution for cutting large blocks of plastic, he turned to Colter & Peterson for a rebuilt 54" SABER cutting system with a custom prep table. In the last six weeks, it not only eliminated reliability problems but has proven to be a user-friendly solution for his growing business.
Tru-Vision uses the SABER and an older 54″ machine to cut different grades of clear PETG, polycarbonate and other plastic substrates for safety and dental visors, including molded parts such as dental retainers. Dean says the dental supply side of his business continues to expand, with the SABER cutting a majority of the 40,000 lbs. of material each month.
“Were using both machines to cut seven different substrates, specifically clear PETG and clarified polypropylene for the dental retainers,” said Dean. A former Union Carbide guy from Texas City, he opened the custom converting company in 1999. Dean now has 12 employees who operate from an 80,000 square-foot manufacturing and warehouse facility that is four times larger than the previous space they moved from in 2012.
“The SABER is cutting 90% of the material and the machine it replaced was from the 1960s. It worked all the time but was getting old, so we looked around but already knew about Colter & Peterson. We used them for spare parts for the other machine and decided to upgrade to a rebuilt, 16-year-old machine. Building cutters is what they do, weve had very few issues with them, and their service is very good. Those are all the reasons why you buy the machine.”
Dean says the speed of his newest cutter is a bit faster, but the biggest differences are the amount of plastic that can be accurately cut at one time and the reduced stress on his operators.
“Our raw product comes to us as 37″ by 48″ sheets. We then stack 100 sheets into the SABER and cut precise 5″ squares for the dental products. We also cut lesser amounts for our aggregate safety products, typically 5″ by 14″ rectangles using polycarbonate or PETG,” said Dean, who indicated the rectangles are cut to create specialty facial visor covers used in the blasting industry.
New technology on the SABER cutting system is giving Tru-Vision a true platform to build on while saving time and effort.
“Depending on the gauge, we cut sheets from 15 mil up to 60 mil in thickness,” continued Dean. “Our biggest volume is 40 mil, and when you load 100 sheets at a time its like a 300 lb. block of plastic. Thats where the SABERs air table relieves our press guys from doing more work. It has a newer design and technology with a faster back gate. It works really well and is much more reliable. You just give the stack a nudge and the machine takes care of the rest.”
Dean expects that as the business continues to grow and his operators become more familiar with the SABER, the new technology will play an even larger role in his companys success.
“Weve only had it six weeks so in the long run, it will tell. Everything we do now goes to the computer interface. Each transition cuts down in time, especially with the programming features. Our previous machine had an old system that was nothing like this. We needed to upgrade and its paying off for us.”