Finishing & Screen Printing
Heidelberg showcases next stage in automated print media production at drupa 2016
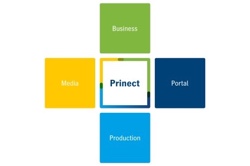
Thursday 17. December 2015 - Prinect digital front end ensures intelligent integration of offset and digital printing
Further automation of mixed form workflow
New Speed Estimator automates costing in MIS
New Prinect Portal integrates online applications
New Prinect Web Shop facilitates move into online business
Automated design creation and precise costing in packaging workflow
Automatic paper stretch compensation for reduced plate consumption and shorter makeready times
Since Heidelberger Druckmaschinen AG (Heidelberg) first unveiled the Prinect print and media workflow over a decade ago, the company has further developed the system to create the basis for virtually fully automated print production. Prinect supports media companies in the smart integration of key print product manufacturing processes. As a result, it already delivers many of the elements and technologies currently being discussed in the context of process digitization and thus forms the basis for the smart print shop – the sector’s answer to the question of Industry 4.0.
Heidelberg will be presenting the next stage in automated print media production at drupa 2016, which is taking place from May 31 to June 10 in Düsseldorf. By continuing to digitize processes throughout the value-added chain of media service providers, the company is significantly improving customer loyalty while also making a major contribution to the sector’s further industrialization.
The main innovations relate to the integration of offset and digital printing in a single workflow, further automation of all production processes, integration of commercial processes, and involvement of print buyers in the workflow.
“As in other sectors, the digitization of key processes is progressing rapidly in the print media industry. Thanks to its Prinect print and media workflow, Heidelberg is able to play a leading role in shaping this process so as to ensure enhanced customer benefits,” says Stephan Plenz, Member of the Management Board responsible for Heidelberg Equipment. “Smart integration is the term we use to describe the essential requirement for becoming a Smart Printshop. What that means is not only greatly simplifying communication between media service providers and their customers, but also making order processing far easier and far more profitable.”
Prinect digital front end ensures intelligent integration of offset and digital printing
The further expansion of digital printing operations is one of the company’s key strategic goals. A major milestone in this respect is the new optional digital front end (DFE) that Heidelberg unveiled in spring 2015, which enables integration of Linoprint digital printing systems with Speedmaster presses in a print shop’s overall workflow. This means all print jobs can be managed and processed centrally in a single workflow system, regardless of the production process selected. The integrated production center that is created combines offset and digital printing systems, each of which can also be operated separately if necessary.
Following a highly successful market launch, Heidelberg is now planning to offer the DFE to other digital print manufacturers. Users will then benefit from also being able to incorporate the digital printing systems of third-party suppliers into their Prinect workflow.
Automated selection of production concept based on job data and product information
The Prinect Smart Automation module is a key component in automated print product manufacturing. For some time now, it has enabled virtually fully automated production of standard print products – from prepress to postpress. Prinect automatically defines the production concepts based on job data and product information.
In time for the upcoming drupa, Prinect Smart Automation will support the fully automated processing of a far wider range of print products. Information about product type and quantity will be read out autonomously and adding the files to be printed will start production fully automatically – all the way through to automatic layout creation. What’s more, Prinect Smart Automation will read out information directly from the data to be printed. This can be used, for example, to control proofer selection in the automated process.
Enhanced process links individual orders from Prinect Business Manager to create production jobs for mixed forms
Based on numerous suggestions from customers, Heidelberg has further optimized the mixed form workflow and, by doing so, taken another big step in simplifying order processing for workflows that are sometimes highly complex. It is now easier to combine the print jobs that lend themselves to production on a mixed form. Once it meets predefined criteria, the production job is automatically initiated and the mixed form can then be produced automatically all the way through to finishing. Users also have the option of preparing mixed forms in conjunction with the Prinect Business Manager.
Efficient production of mixed forms offers particularly significant customer benefits in the packaging sector, where utilizing even a few millimeters more of each sheet has a big financial impact.
Speed Estimator automates costing in Prinect Business Manager
A growing number of customer inquiries, ever shorter print runs, and possibly smaller margins mean that print shops need to significantly reduce the amount of work involved in completing individual customer projects. The new Speed Estimator, which forms part of the Prinect Business Manager MIS solution, now makes this far easier thanks to fully automatic costing of the entire production concept, the layout, and the outlay for standard products. The products requested are defined in a matter of seconds in a user-friendly, browser-based input mask in the new Prinect portal. The Speed Estimator compares all the production options available in the print shop for this product and automatically selects the most suitable. While most web shops involve simply selecting an item from a price list, the Speed Estimator automatically defines the entire process network and layout with an accurate costing that is always up to date. This also forms the basis for automatic job creation in the subsequent Prinect production workflow.
In conjunction with the new Prinect portal, the amount of work involved in processing customer inquiries, preparing quotations, and creating jobs for production can be significantly reduced – in the ideal-case scenario by up to 90 percent.
New Prinect Portal integrates Prinect online applications
The new Prinect Portal, which will be available from drupa 2016 onward, facilitates communication between customers and service providers. Print shops give their customers personalized online access and the relevant authorizations can be customized. This is intended to make the Prinect Portal the standard tool for completing all key steps in the workflow – from customer inquiry and quotation costing to production, delivery, invoicing, and evaluation. In the future, the Prinect Portal will enable customers to ascertain and manage the status of their print jobs online at a glance at any time without having to install additional software. They will be able to see whether a quotation has already been provided for jobs they have inquired about, which jobs are at which stage, and for instance whether an approval is required. Any approval needed can then be given straight away online or further corrections can be requested. What’s more, repeat jobs can also be started from the portal if necessary.
Print shop staff can also access this data and manage jobs via their browsers in line with their specific authorizations. This means, for example, that field staff who are visiting customers can call up orders, prepare new quotations, and discuss real-time processes directly.
Customers benefit from a personal portal that provides them with all the data relating to their print jobs at a glance and makes communication with the service provider much quicker and easier. Print shops, for their part, can reduce the amount of work involved in processing print jobs and manage orders remotely, in consultation with customers if necessary.
The Prinect Portal is structured so as to enable the future transfer of further functions and tasks from software that was previously managed locally to the browser-based tool, thereby opening up completely new ways for print shops and their customers to work together easily.
New Prinect Web Shop facilitates move into online business
The new Prinect Web Shop is a software-as-a-service solution from Heidelberg and augments the Prinect portfolio for incorporating media service provider customers into the workflow. The new web shop also forms a fully integral part of Prinect, which ensures automatic exchange of all necessary information between shop, MIS, and production system. The solution aims to make it easy and uncomplicated for SMEs to move into online business.
Automated creation of design structures and precise costing data for packaging
Heidelberg also ensures intelligent integration of key production processes in packaging printing. From the upcoming drupa onward, integration of the Prinect Package Designer CAD software will enable packaging printers to fully automate the creation of standard designs such as ECMA and FEFCO and customer designs. Once the product code has been selected, the carton dimensions have been entered, the substrate has been selected, and the available machine formats taken into account in the MIS or Prinect cockpit, both the contour of the individual repeat and the appropriate sheet layouts are generated automatically, without the need for any intervention on a CAD system. In addition to the CAD data required for die production and the production job, precise administrative details are also provided in a matter of seconds, including the number of repeats on each sheet, the minimum sheet format, the number of sheets required and the dimensions of the product. This data can be provided directly for costing and production planning purposes – even if the design is prepared manually. This not only saves time, but also eliminates errors and inaccuracies.
Automatic paper stretch compensation for reduced plate consumption and shorter makeready times
The physical properties of paper represent a particular challenge in offset printing. During the printing process, mechanical influences affect the extent to which print sheets stretch. The larger the sheet format and the higher the number of printing units being used, the more pronounced the effect is. Unless steps are taken to compensate for this, register inaccuracies occur and the print result is highly unsatisfactory. Existing compensation processes are complex. Heidelberg already offers the paper stretch compensation function for Speedmaster presses. This function automatically corrects the image data output for a print job that has already been produced and saved in the system, which means the correction process can be incorporated automatically for a repeat job.
To coincide with the upcoming drupa 2016, Heidelberg is launching the new automatic paper stretch compensation function. The degree of paper stretching associated with the relevant paper type and job specification is automatically simulated in the software and the corresponding corrections are applied to the image data being output. This produces an impressive print result from the outset without any prior plate output or measurements on the sheet. It also leads to a far more efficient production process, cuts makeready times, and significantly reduces printing plate consumption.
Figure
To coincide with the upcoming drupa 2016, Heidelberg is enabling smart integration of further key processes of media service providers by adding new functions for the print and media workflow.