Packaging
The unique features of the SACMI IPS at the Plastimagen 2023 exhibition
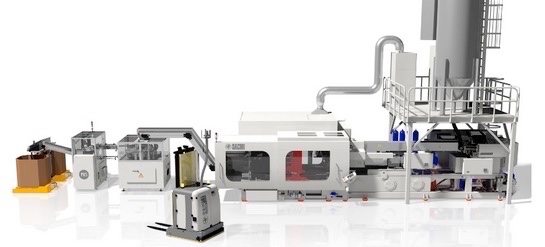
Friday 08. December 2023 - SACMI de Mexico makes a dedicated team of technicians available to provide service and support for its leading technologies, CCM (continuous compression moulding) for caps and IPS (injection preform system) for preforms.
Strategic in terms of volumes and the number of projects, Mexico speaks the language of SACMI innovation. How? Through a unique offer, ranging from quality control integrated in the IPS presses to the possibility of increasing productivity of the new lightweight necks that are currently in high demand on the market
An unparalleled proposal for the Mexican market. SACMI brings it to Plastimagen (7-10 November 2023, Centro Citibanamex, Mexico City), an international plastic processing exhibition for the food and beverage industries.
With more than 90 machines supplied to the leading players in the sector, Mexico confirms itself as a strategic market in terms of volume and the number of projects implemented by SACMI.
These include newly acquired references in the supply of injection moulding machines for preforms, which complement its consolidated technological leadership in the cap machine market.
The SACMI De Mexico team
A distinctive feature of SACMI is its in-depth knowledge of the market and its extensive support service and facilities throughout the world. SACMI de Mexico makes a dedicated team of technicians available to provide service and support for its leading technologies, CCM (continuous compression moulding) for caps and IPS (injection preform system) for preforms.
The exhibition space of our local agent Plasgrom provides an opportunity for you to get to know the SACMI team and learn about the main technological advantages of the offer.
Preform Vision System, an exclusive feature of the SACMI IPS
With the IPS range, SACMI has thrown down the gauntlet to the preform production technology market, strengthening its consolidated leadership in the caps segment. The latest developments include the first range of solutions available on the market capable of integrating quality control directly into the press.
Available as an optional on the IPS 300 and 400, the PVS156 system produced by SACMI Computer Vision System allows as many as 96 preforms to be inspected in just 5 minutes. The main advantage is its ability to detect process deviations in real time, thereby avoiding non-conforming or incorrect batches.
Increased productivity (for the new 26/22mm necks)
With the IPS, productivity can be increased for the same tonnage. This unique opportunity refers specifically to the production of the new ‘lightweight’ preforms for 26/22 mm, GME 30/40 and 30/41 necks.
The higher pitch of the IPS compared to alternative solutions on the market and the availability of the new high-cavity moulds, supplied exclusively by our partner MHT, allow SACMI to increase the number of cavities from 96 to 128 on the IPS 300 and from 128 to 144 on the IPS 400. This is practically equivalent (for this specific set of standards, which are currently among the most popular on the market) to the productivity that can be achieved by a 500-tonne press.
References and service
It is these distinctive factors – the opportunity of integrated quality control and high productivity with reduced consumption – that are at the basis of the new references acquired by SACMI in Latin America, a highly developed market characterised by high specialisation and a focus on innovation.
In addition to the technological advantages, the new ‘SACMI Smart Services’ are highly appreciated by our customers, which mean they can take advantage of the new preventive and scheduled maintenance plans.
Zero downtime, zero worries, and being able to focus on one’s own business are some of the advantages of this improvement in the support services, which are always provided in synergy between the Italian parent company and the local SACMI facilities, and which also make use of the new digital platforms.