Inkjet & Digital Printing
Improve efficiency with workflow automation
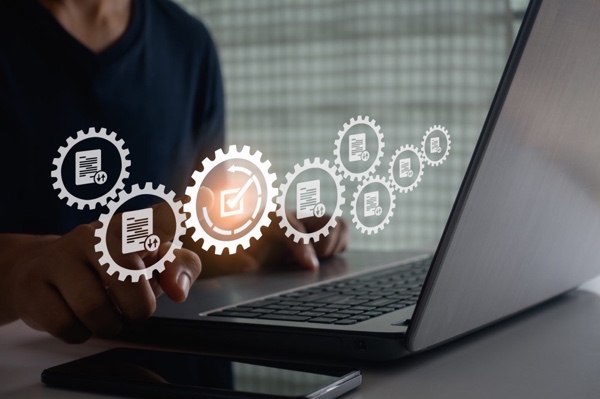
Wednesday 25. October 2023 - creating disparate islands of automation. New technologies will enable some PSPs to excel beyond their competitors, adding services and improving outputs. But others run the risk of crumbling under the complexity of bolting on more and more new tools to an old process that cant support them.
By Juergen Krebs, Software Sales Manager, Ricoh Graphic Communications, Ricoh Europe
The print industry is changing. Efficiency is everything. The faster jobs are processed, printed, and delivered, the greater the production capacity, the higher the earnings potential and the happier clients are.
The efficiency of today’s Print Service Providers (PSPs) is significantly challenged by increasingly complex print workflows resulting from much needed portfolio additions. New hardware and technology are often bolted onto existing systems and workflows, creating disparate islands of automation.
New technologies will enable some PSPs to excel beyond their competitors, adding services and improving outputs. But others run the risk of crumbling under the complexity of bolting on more and more new tools to an old process that can’t support them. Over time they can struggle with this grow as you go approach that leads to a messy, convoluted process.
A workflow analysis can help print businesses understand what’s happening in their workflows, identify redundancies and inefficiencies, and ultimately chart a better course based on a holistic workflow plan.
It spots the weaknesses, choke points, and potentially unnecessary steps in the process to help craft a plan that resolves the issues identified.
There are seven basic steps:
1. Document current workflows and processes
Before starting to improve workflows, operations should understand what they are, and senior staff should agree. It’s all too common for various department heads to work from different understandings of how a process should work, quickly leading to dysfunction. It is a good time to visually map out the existing process and define each step along the way. If this has been done before, now is the time to revisit previous work and update it to fit how the business is working today. Having a cadence for continuing checks and balances to map the journey is important for the whole team to set expectations with milestones and transparency on changes and improvements.
2. Identify pain points and problems
Somewhere between the beginning of phase one and the end of phase two, compile a list of pain points and problems that the workflow should plan to address. Some of these will be obvious. Others will become apparent when the leadership team disagrees during that process. And still, others won’t appear until more data is gathered.
3. Gather more data
During this phase, the “what” questions that the first phase created should be answered.
Both quantitative (numerical) and qualitative (descriptive) data on the various pain points and problems and on the workflow and process steps identified in the first phase should be collected. Quantitative or hard data is objective, usually numerical: how much time is job setup taking? How much faster does production need to go? What factors contribute to delays on a specific piece of equipment? Qualitative or soft data is more subjective: how does this problem affect the success of your sales staff? What are the implications of job setup taking this long? Is that specific subtask necessary? What are the benefits and risks of automating a set of manual steps?
4. Analyse the data collected
Once the “what” data has been collected, the “why” needs to be answered and the questions it generates. For example:
Why are we hitting these bottlenecks?
Why does job setup take as long as it does?
Why are we repeating manual data entry?
Also prioritise which of the identified issues are critical and which can be left alone for now.
5. Identify the changes to be made
Once the problem and the reason for the problem is identified, it’s time for the “how” question: how will it be fixed? To answer “how” questions effectively requires careful thought, brainstorming, sometimes trial and error, and sometimes consulting and professional services.
6. Implement identified changes
Once changes have been chosen, it’s time to implement them. Don’t forget staff education here: when changing processes, people need to know (and be shown how to operate in the new process).
7. Follow up
A workflow analysis is not a single event. PSPs will need to re-evaluate sometime after implementation and do the process again. It shouldn’t take as long this time, but there might be a new set of issues that will need to be worked through.
When considering what methods and strategies will lead to results for improving workflow efficiency in commercial print look at ways to:
Automate repetitive processes.
Minimise or eliminate manual data entry and rekeying.
Streamline your order entry with a web to print (W2P) portal.
Use better print production management software.
A workflow analysis may discover the problem isn’t the process but the software powering that process. RICOH Supervisor is the modern print production management software solution built for the future of print. This cloud-based, vendor agnostic platform gathers and interprets data from sources throughout print workflows, providing insights required to answer the “what” and “why” questions and helping steer operations toward the “how.”
So “what” are you waiting for? “Why” hasn’t RICOH Supervisor been added to your software portfolio? Speak to a Ricoh representative and see “how” it could be the key to unlocking unprecedented productivity and profitability.