Finishing & Screen Printing
The Zünd Cutter G3 L-2500 Runs like Swiss clockwork
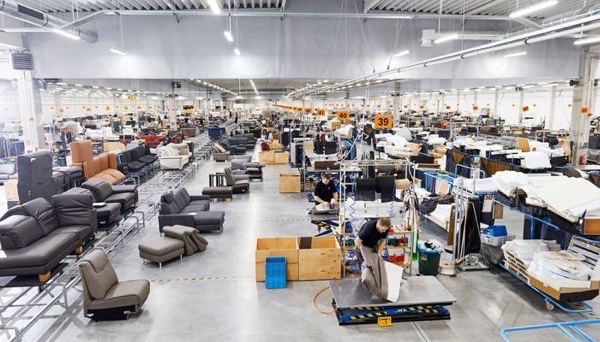
Tuesday 07. September 2021 - The 3C Group from Rheda-Wiedenbrück is one of the largest suppliers of upholstered furniture to the German and European furniture trade. In their production plant in Krupina, Slovakia, a Zünd Cutter G3 L-2500 has recently been put into operation.
Behind the three Cs are their two large sales lines, Candy and Carina, as well as the Contract division. Today, 3C manufactures its collections in four of its own production facilities in Poland and Slovakia. Production is for the German and international markets. From the first sketches to sample production, production and logistics, everything remains in one hand.
And business is good. Founded in 1991, the group has been growing steadily for years and has positioned itself for the future with targeted investments in state-of-the-art production technologies. Today, the 3C Group employs around 200 people at its headquarters and 1800 in Poland and Slovakia. Digital technologies and a high degree of automation, for example in fabric and leather cutting, are a matter of course. The high level of digital competence combined with top-quality upholstery craftsmanship is then also one of the reasons for the company’s continuing success. As early as 2012, the first fully integrated cutting lines were set up.
Easy integration into existing workflows
The textile or leather covers are cut to size on state-of-the-art cutting systems. This includes the latest digital cutting technology from Zünd, for maximum production flexibility and cutting efficiency. A Zünd G3 L-2500 cutter was recently commissioned at the 3C Lind plant in Krupina, Slovakia. One of the goals was to sustainably increase cutting capacities, explains Franz-Wilhelm Walter in an interview. Walter is a member of the company management and responsible for production and IT: “Increasing capacity was one of the goals of this investment, which was incidentally achieved. More important was and is the fact that Zünd cutters can be implemented very easily in existing workflows. This is an important factor in our highly networked and integrated production cells. Combined with the fact that we didn’t have to adapt our planning structure in the slightest.”
The initial impetus for the investment, however, came from another point, namely the handling of sensitive data. In the course of digitalisation, all templates have also been digitalised and are stored digitally on local servers (tried and tested technology). This has the great advantage that analogue stencils no longer have to be stored. But now the question arises as to the correct, i.e. secure, interim storage of this data. Walter explains: “We have had intensive discussions with those responsible at Zünd about the correct handling of sensitive data. Their cutting solutions have an open system architecture. On the one hand, this has the already mentioned advantage of their easy integration into existing workflows. But it also means that Zünd does not impose any requirements on us when it comes to data handling. An enormously important point for us. In short, we were looking for a partner who ticks similar boxes to ourselves. And we wanted a partnership based on stability. We found both with Zünd.”
But the fact that those responsible for cutting technology chose Zünd was also due to the cutting systems themselves as well as the production reliability and availability. Says Walter: “The Zünd G3 cutter is also convincing across the board in terms of machine reliability. The same applies to the quality of the cut and its overall productivity – combined with low demand for consumables and wear materials. And last but not least, we have experienced very professional project support from Zünd and place the highest trust in their competencies.”