Finishing & Screen Printing
Jash Packaging plugs demand-supply gap with two BOBST folder-gluers
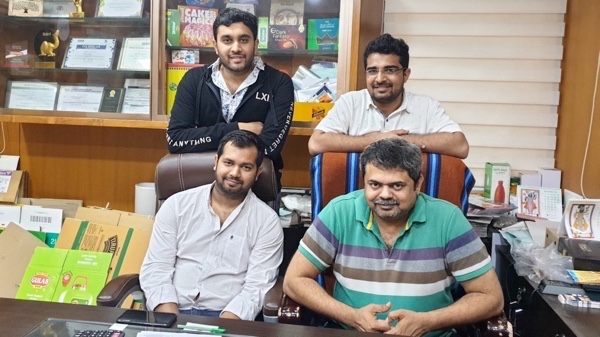
Wednesday 19. August 2020 - Packaging specialist Jash Packaging invested in two BOBST folder-gluers - a VISIONFOLD 110 A2 and an AMBITION 76 A1 - a few months ago in a bid to continue its 20% year-on-year growth. The Vadodara-based 50-year-old company installed the two machines at their companys folding carton unit in the city, along with two of their existing BOBST machines - a BOBST folder-gluer LILA II 145 A2 and a NOVACUT 106 E die-cutter.
The company is currently converting around 4,000 tonnes in corrugated and about 1,000 tonnes of solid board per month. According to Ravindra Patel, proprietor of Jash, there was a demand-supply gap, as a result of which the company faced difficulties in delivering the volume required by the customers on time with the existing gluers. “We decided to ramp up the finishing capabilities and bolstered the two existing folder-gluers with the addition of two new BOBST machines,” said Mr Patel, who is assisted by his son Kishan in running the business.
The AMBITION 76 A1 features a straight line open width of 76 to 760 mm, lock bottom open width of 146 to 760mm and a running speed of up to 300 m/min, while the VISIONFOLD 110 A2 features a straight line open width of 76 to 1,100 mm, lock bottom open width of 146 to 1,100mm and a speed of up to 350 m/min.
“Both machines are capable of running straight line, crash lock bottom, disproportionate outer cartons and litho laminated three-ply cartons. The VISIONFOLD 110 A2 is in addition equipped with to run specialty four- and six-corner jobs. Consistency and faster job changeovers allow the customer to achieve more production in the given time,” said the Regional Sales Manager – Western region, India at BOBST.
The company additionally installed HANDYPACK on both machines. It is a kit that is installed at the delivery section, which according to Mr Patel, increases the productivity of the folder-gluer through easy carton collection, resulting in optimum utilisation of the folder-gluers and minimising the manual labour required at delivery – a wonderful example of automation.
Mr Patel said, “Increasing the total capacity to offer prompt service to our customers was our main requirement. We looked at the machines manufactured in the Far East, and found they were slower compared to the one from BOBST.”
He added, “We have had a good history of growth. Times are tough, but one has to be aggressive and pro-active as well as vigilant and shrewd, to continue the streak of success. In our endeavour, we relied on BOBST because of its prompt service, the process support to hand-hold us and to get the machine to reach its optimum level of performance. This has really boosted our production level substantially compared to what we were able to achieve earlier.”
In todays competitive world you need machines that can produce more in less time with less manpower and this is where a BOBST machine can add value.