Offset Printing
How BOBST machines support the flexible packaging and labels industries to ensure business continuity
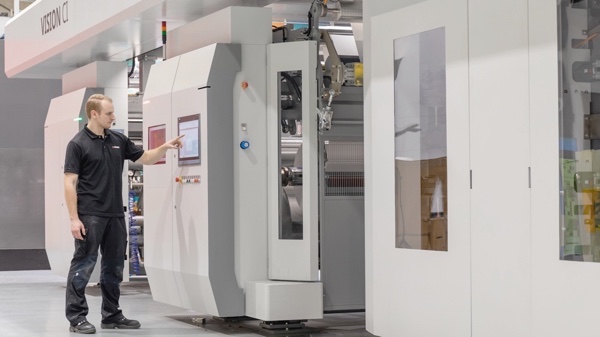
Tuesday 07. April 2020 - Packaging converters are going through tough times. Not only due to the coronavirus crisis, but also due to the high demand for flexible packaging and labels that has been one of the consequences of it as retailers try to keep pace with consumer demand.
This unexpected situation raises the following questions:
How to maintain business process stability
How to react quickly to changes of capacity
How to ensure production capabilities, productivity and product quality
How to remain competitive answering client needs
To cope with the above, many converters have built dedicated “crisis teams” and related “business continuity plans”. Such plans are effective for management to take the right decisions in the given circumstances but when the crisis is over, it will leave behind one challenge that will never go away: having no orders or too many orders.
The challenge for a smooth and flexible operation is to manage three major Key Performance Indicators
) Machine availability
) Operator availability
) Material availability
At BOBST, we are working with our customers to help maintain all three.
We are a true partner for our customers at all times, not only when the sun is shining – we have built machines and processes to ensure solid operations that can remain robust throughout the years, even during times of crisis. We prove this every day with our global Remote Services and Connected Services, optimizing machine availability.
Of course, machine availability is one factor that can keep our customers awake during the night in challenging times but another critical success factor is operator availability. To maintain levels of quality and productivity, it is important to have the right operator, in the right place at the right time. In times of crisis, where you cannot be sure of having all the operators available all the time, you still need to ensure you can deliver at the usual levels of quality, punctuality and cost.
The way to ensure this is operator flexibility and interchangeability. In an ideal and theoretical world, you would only need one type of machine, one single technology, and one standard Human Machine Interface (HMI) on all machines. One quality control system, one maintenance routine. But who lives in that world? Nobody, at least not that I know.
At BOBST, we build solutions to ensure operator flexibility and interchangeability. How do we do this?
We are the only supplier in the flexible packaging industry who covers the full value chain with our complete machine portfolio. From vacuum metallizing, wet coating, inline flexo printing and converting, CI flexo printing, gravure printing, hybrid- and digital printing and lamination, we provide machines designed with the same principles, same electronical parts, same HMI, same maintenance principles. It is therefore much easier to cross train the operators on several technologies and distinct machines. In production management, process and machine standardization is a key element to ensure a high level of productivity and quality.
But of course, not every operator can be a process expert across all application processes. To make our machines less dependent on operator knowledge and to ensure top quality and productivity no matter how well the operator is trained in the process, we rely on the digitalization and the automation of key processes across labels and flexible packaging. The solutions you need to look at exist today and will matter even more in challenging times. BOBST has developed breakthrough solutions such as DigiColor and Ink on Demand for narrow web flexo printing to automate the entire flexo printing process. In gravure printing, we provide the TAPS function for an automatic register setting without operator interaction. In CI flexo, we built the new easy SmartKey solution on the Vision CI, similar to SmartGPS.
In our Competence Centers in Italy, Germany, UK, Switzerland and China we are not only offering our machines for tests, demos, product development and sample production, we are also offering special training for your operators to boost your productivity. You can easily train your operators on several technologies and several machines, ensuring they are ready when the unexpected happens.
Raw material availability is the last important element to ensure your production is always up and running. Especially if borders are closed and you need to find alternative materials. The BOBST Registron technology helps you to cope with various substrate types and calibration through ultra-precise web handling.
In these times when we are practicing social distancing, it feels as though we are all coming closer together. For us in BOBST, all of our customers are partners or even family members. So, we want to take care of you now all the time with meaningful innovations. Whether its now, once the crisis is over, or while working on your packaging production capabilities, do not hesitate to contact us any time. We will be stronger together. Take care and stay safe!
Christian Zeller
Strategic Product Marketing Director, BOBST