Inkjet & Digital Printing
An Explosion of Possibilities in Direct-to-Object Cylindrical Printing
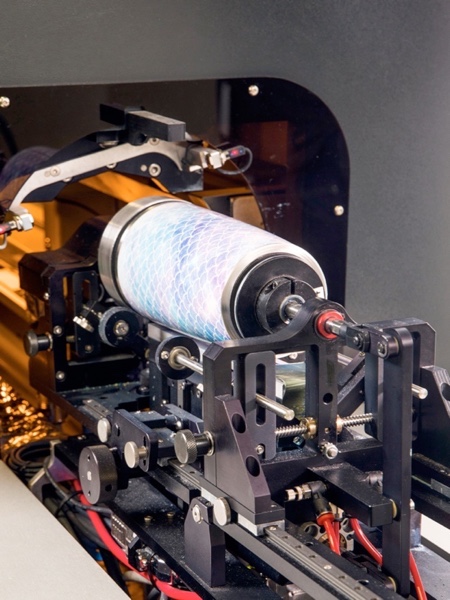
Monday 24. June 2019 - New product applications, combined with digital technology-driven printing techniques including speciality inks and advanced printheads, have opened up a range of creative expressions for DTO cylindrical printing. Even better, the process is now highly automated, with impressive quality, at a more cost-effective price point.
Direct-to-object cylindrical printing is a comparatively new technique in which a device directly lays ink onto a spinning, curved surface at a rapid pace. Printing on cylindrical objects can be achieved using either pad or digital printing techniques. Pad printing is suitable when the job calls for one or two colours over a limited (non-wrap around) area, typically less than 25% of the surface. Digital printing, by comparison, can produce beautiful full-colour, full-wrap images.
To screen or not to screen
DTO cylindrical printing has traditionally been done using screen printing methods. Screen printing has the advantage of widely installed equipment and a well-practiced technique, but is disadvantaged in labour time, material costs and additional production steps. As cylindrical jobs include more colours and creative imaging options, screen printing is being supplanted by more efficient and capable digital systems.
DTO digital offers three main advantages over screen printing:
1) It can produce multiple colours and/or design effects in one pass
2) It has the ability to print short runs with customisation
3) It has significant time and cost savings.
All together, these strengths make for a compelling case.
Abundance of applications
While digital printing on flat objects has been a standard industry practice for years, users can now digitally print on an expansive range of cylindrical items. Inkcups (www.inkcups.com) offers the Helix, Helix Hi-Fi and X360 rotary inkjet printing systems for this purpose.
Its important to note, however, that many machines on the market restrict what type of cylinder the printer can handle. Some key considerations are printable diameter, length of the object and depth of the largest contour. In addition to machine limitations, users should also take into account the composition of the item, as certain inks can only properly adhere to specific substrates.
Among the many cylindrical items that can now be digitally printed are glass and barware; stainless steel and plastic sports bottles; candles and candle holders; industrial tubes; disposable cups; beer and spirit bottles; measuring cups; event-based products (i.e. water bottles for bicycle races); personalised items; and cosmetics. In addition, this method can print on a variety of materials including glass, coated metals, stainless steel, plastic, paraffin wax (candles), silicone and rubber.
Glass objects for instance are becoming increasingly popular. For glass, items must first be flame-treated to remove impurities and any “cold coating” from the surface, then treated with primer to allow the ink to properly adhere. Inkcups Magicoat is one of two glass primers on the market for this purpose. Other trending DTO-printed cylindrical items are triton plastic (e.g. nalgene bottles) and bicycle bottles – especially “extreme squeeze” types, which must retain their artwork through hundreds of uses. Inkcups digitally printed inks are highly durable and abrasion-resistant (e.g. up to 500 washes for glassware) and meet ASTM International standards for adhesion.
Colour and design variety
The ability of DTO digital machines to print full colour in one pass, including primers, varnishes and specialty inks, enables a wide spectrum of design techniques. These include:
Mirror prints: viewable on the inside and outside of glass or plastic
Tone on tone: solid matte-finished substrate enhanced with one ink or clear coat
Stained glass: colour opaque enough to see through
Contouring
Etched
Full-wrap cylindrical printing also demands seamless borders with no visual “lap mark.” For added flexibility and ease of file preparation, original graphic artwork should be able to be imaged on cylinders and tapers without the need for manipulation or distortion i.e. flat images will print to scale on a curved surface, with software automatically making the adjustment. The best machines on the market will easily handle these requirements.
Full-colour DTO digital is by definition a faster process than screen printing, thanks to fewer production steps. Theres less set-up time for multiple colours and more complex jobs, which enable reduced run lengths. This means that users can better manage inventory by producing smaller, on-demand runs, as well as respond to time-sensitive demands, such as quick-turnaround jobs tied to sports competitions, significant events or celebrations.
What to look for
When shopping for a DTO digital printing solution for cylindrical applications, consider the types of objects and materials youll be printing on, as well as the range of colours and design techniques you might encounter. Not all inks are created equal, so be sure to evaluate quality and durability on different items (asking for test samples is always a good idea). Make sure your equipment supplier understands the unique needs of your market and can provide testing, direct sales support and expert advice. Inkcups Europe GmbH, based in Freudenberg, North Rhine-Westphalia, Germany, covers this complete range of requirements and products.
With these considerations in mind – and the right partner for hardware, consumables and service – youll be ready to set off your own explosion of market opportunities.