Offset Printing
Cartonajes Santorromn installs the first BOBST Digital Inspection Table in Spain
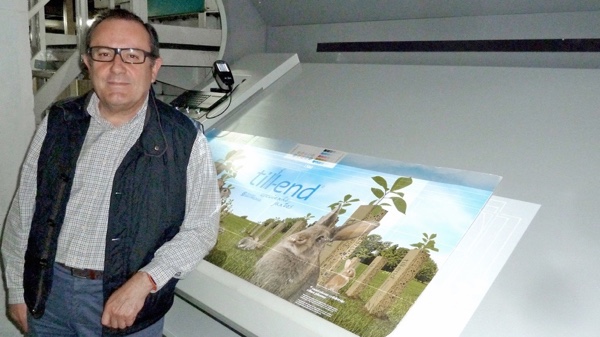
Tuesday 18. June 2019 - Since then, many BOBST machines have been installed. These include five flatbed die-cutters - SPO 1575, SPO 160 VISION, two SPO 160 A MATICs and MASTERCUT 1.7 - one PACIFIC folder-gluer, a MASTERFLEX 203 A MATIC flexo post-printing press and two Digital Inspection Tables, which were the first to reach Spain. In addition, a MASTERFOLD 170 will shortly be installed.
Jesús Pérez, Technical Manager at Cartonajes Santorromán, explains that “the company’s philosophy is to constantly invest in infrastructure and technology for the manufacturing of corrugated board, as well as in any product that can be made using this material. We therefore have four plants in Calahorra, two for production and the other two for services. The total area is over 60,000 m2 and the manufacturing capacity is over 50,000,000 m2 of corrugated board per year, mainly destined for food and drinks packaging. Leopoldo Santorromán, the Manager of Cartonajes Santorromán and current president of the AFCO association, ensures that the philosophy of the four-generation family dynasty with a history of over 100 years is carried on to the next generation.”
This philosophy also favors customer service, which even prevails over production, as it is one of the few companies in the country that can offer services from one day to the next. To be able to do that, Mr. Pérez explains that they are technologically prepared to have 25% manufacturing capacity available to cover this type of order. The inclusion of the new MASTERFOLD 170 responds precisely to the need for more capacity.
“Our aim is to satisfy our customers, so we order the rolls, paper qualities and everything the customer requests. If the machine has to be stopped, so be it, and if waste has to be increased, that too. Our advantage is that we have the necessary means to optimize this different way of working and specialization in service is our strong point,” explains Pérez.
BOBST Digital Inspection Tables
In 2018, Cartonajes Santorromán installed two BOBST Digital Inspection Tables, within three months of each other. Their function is to check the register between printed material, die-cut blank and artwork. It includes the possibility for a user to plug his existing spectrometric solution to the BOBST Digital Inspection Table in order to add the color analysis to be added to the same quality check report. The first BOBST Digital Inspection Table was installed for the companys MASTERFLEX 203 A MATIC. For Mr. Pérez, the change has been tremendous as all the checks are now grouped together proving that the inspection plan has been carried out properly.
“Before the arrival of the BOBST Digital Inspection Tables, everything was done manually. Working off-line we used Astralon foils, which are transparent drawings for control of the die-cut blank, but Astralon foil would deteriorate over time or be lost. This no longer happens with the BOBST Digital Inspection Tables. It has also been possible to digitize the work flow between the artwork / design department and the production department. This means that all information relating to production – such as the final artwork, colors, the printing presses and the anilox rollers to be used, etc. – can now be included in the customer’s quotation. This change has meant that commercial errors are avoided,” explains Pérez.
With the BOBST Digital Inspection Tables, the quality check is digitalized and all the checks are grouped together without the machines having to be stopped. Each table serves two and a half die-cutters, which for the moment is sufficient for the company’s five die-cutters. For the Technical Manager of Cartonajes Santorromán, this is a huge step forward as delivery quality can certainly be improved for the customer, and it is guaranteed that what is being printed corresponds exactly to what was agreed.
The BOBST Digital Inspection Table incorporates digital projection for the proofing of printed artwork and die-cut blanks, whilst providing real-time visual representations to match the product with digital proofs. It uses HD projectors to illuminate the product sample with quality control imaging, enabling the operator to easily see if quality standards are matched or compromised. In addition, the layout file can also be projected on to the sheet so that print registration can be checked and adjusted. This removes the need for overlays, print minis and moving the process from paper to digital.
Mr. Pérez explains that it is easy to install and operate the tables. “The BOBST experts installed the Digital Inspection Tables in a couple of days, and after a two-hour instruction, our operators already knew how to operate them. In addition, BOBST has remote access to the tables and that is reassurance for us. We have also been able to reduce the number of machine personnel, from three persons to two persons per shift, freeing up staff time for other tasks. Our expectations are met and the hoped-for benefits in terms of quality and productivity have been achieved. We certainly recommend the table.”
At Cartonajes Santorromán, the operators are using the BOBST Digital Inspection Tables in the following way: First, they check that the print matches the die-cutting layout, and, at the same time, the color is also checked. If needed, the color register is corrected. After that, the warp analysis and color adjustment are performed, as are any checks specified in the inspection plan. The operator simply projects the print onto the printed sheet and in half a minute the sheet is checked.
Pérez says that “finer adjustments of color and the print were previously checked on a computer screen, whereas now it is projected and magnified. The BOBST Digital Inspection Table can even digitally project the bar codes. Without doubt, with a production of 1,700,000 sheets a month and thanks to the BOBST Digital Inspection Tables, a huge amount of time is saved compared to previously, and the quality guarantee is indisputable.”
MASTERFOLD
Another recent purchase by Cartonajes Santorromán is a MASTERFOLD 170 folder-gluer which will shortly be installed. Mr. Pérez explains that such an investment was necessary to have more margin of manufacturing capacity available for carrying out last-minute orders. The MASTERFOLD was chosen because it allows fast make-readies and delivers high productivity, as well as for the good service and reassurance that BOBST is offering. “We were looking for a robust machine at the right size for mid-format production. Our production is now more effective and efficient, because MASTERFOLD enables us to improve programming and maintain the availability percentage. Our aim is to produce 15,000 units per hour with this new equipment.”
For Cartonajes Santorromán, investments enable them to provide better service and quality to the customer, which form the basis of the company. They therefore ensure to continue investing. Consequently, Mr. Pérez is already thinking of incorporating another BOBST Inspection Table for another machine which prints high-quality coated carton and later on an MASTERFLEX-HD flexo post-printing press. “We are convinced that the corrugated board world will continue expanding and that there are many opportunities. But for this, it is necessary to invest, to research new areas of corrugated board use and to offer new services to our customers.”