Offset Printing
Seaway Invests in Heidelberg Technology to Solve Customers Supply Chain Challenges
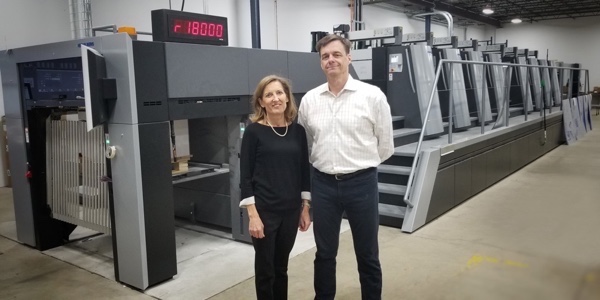
Wednesday 27. February 2019 - Seaway, a world-class printer of specialty and bound products based in Green Bay, Wisconsin, is delivering its fastest turnaround times for customers to date by adding the Heidelberg Speedmaster XL 106-8P, with LED UV drying, to its printing technology capabilities. With the new XL 106, Seaway will continue to supply the high-quality products its customers expect while reducing its energy consumption at the same time.
“Seaway is always looking for new ways to contribute to our customers success and, in order to do that, we invest in Heidelberg innovations that make us a printing operation they can trust to provide quality work with quick turnaround times,” said Kevin Heslin, President of Seaway. “Since weve installed the Speedmaster XL 106-8P in October 2018, weve generated more than 11 million sheets with the press, using its complete spectrum of UV applications.”
After steady yearly growth of 18 percent for the past five years and reaching production capacity, Seaways investment in new Heidelberg technology ensures continued expansion with lower manufacturing and energy costs as well as improved quality. Running alongside a three-year-old XL 106-4+L, the new Speedmaster XL 106-8P is 2 1/2 times more productive than the XL 105 it is replacing, thanks to the enhanced press features.
The XL 106s game-changing Push-to-Stop technology allows jobs to be autonomously switched over without operator intervention and is powered by Intellistart 2, which carries out the next steps in job preparation – reducing Seaways labor needs, improving project speed and efficiency, and limiting operator error. The result is a consistent, high-quality product, no matter the operator, that satisfies Seaways customers and eliminates costly rework.
“Since investing in the Heidelberg Speedmaster XL 106-8P, weve seen consistent maximum production of 18,000 sheets per hour,” Heslin said. “Push-to-Stop automation capabilities, coupled with the units ability to print on both sides in one pass, greatly shorten make-ready times and allow us to move sheets straight from delivery to bindery. Not only does this create greater capacity, but it allows us to take on more work as demand arises. We expect the Push-to-Stop feature alone will increase our productivity by 25 percent.”
Seaways Speedmaster XL 106 includes DryStar LED, the most advanced drying technology on the market. The zero dry time provided by DryStar LED allows for a faster throughput and cuts energy consumption in half due to (A.F.S) Automatic Format Setting and Instant on/off technology compared to other technologies. Production generates zero emissions, does not produce ozone or infrared radiation, and is odorless, all of which supports environmentally friendly production. The LED technique provides a rich color depth and brilliance – even on uncoated papers – that cannot be attained by conventional printing.
The press can handle a wide range of substrates and includes the new CutStar roll sheeter, which answers the industry trend of thinner materials, more make-readies and lower piece counts. The XL 106 press includes AutoPlate XL with Prinect Inpress Control that adjusts registration and color automatically allowing Seaway to hang eight plates every four minutes in approximately 150 sheets of make-ready.
“Heidelberg equipment allows us to contribute to our customers success and growth with high-quality products, service, and faster turnaround times,” said Heslin. “Seaways partnership with Heidelberg is reliable and has contributed to our continued growth year over year. We trust that Heidelberg equipment will consistently deliver only the best results.”
The Speedmaster XL 106-8P is one in Seaways suite of Heidelberg equipment and technology, which includes Prinect Pressroom Manager, an XL 106-4+L, a Stahlfolder TH 82-P and KH 82-P, and a POLAR Cutter System 200.