Finishing & Screen Printing
MPS Leicester invests in efficiency with BOBST
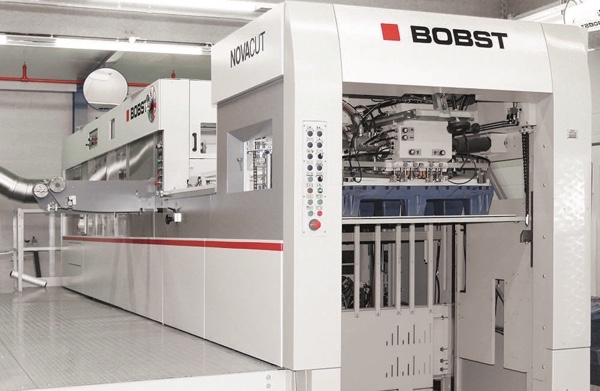
Wednesday 22. August 2018 - As market leaders in the design and printing of folded cartons, labels, inserts and rigid packaging for the branded and healthcare market sectors, MPS Leicester places great emphasis on accuracy, security and staying ahead of the counterfeiting market.
Recently acquired by US packaging giant WestRock, MPS Leicester has a 220-strong workforce at its Leicester site, as well as a Swadlincote distribution centre with over 20,000-pallet capacity.
Customer ordering flexibility is maximised to meet the variable needs of the market – whether it’s the hay fever or flu season – and lead-times are kept short as a result of the companys strategic investment strategy, thus giving the sites the ability to deliver on a consistent basis.
The brief
As market leaders, MPS understands the importance of focus and commitment when it comes to supplying the often complex and fast-moving healthcare sector, and the need for strategic development at the Leicester site to ensure continuity of its success.
With this in mind, the company wanted to invest in a new die-cutter to meet the emerging needs of the market, as well as to minimise make-readies and drive efficiency.
Mark White, MPS Leicester Operations Director, said: “Packaging converters face great challenges when supplying the complex and fast-moving healthcare sector and the risk of getting it wrong can be high.
“Brands are demanding new security features to stay ahead of the counterfeiting market and additional functionality from their packs, for example integral fittings, tagging or RFID. Packs often require inserts, as well as new graphic or tactile effects.
“We are also seeing more legislative requirements, so the printers job is becoming more challenging. It was therefore critical to our operation that this technology investment enabled us to meet these emerging needs.”
What was achieved
BOBST NOVACUT 106 ER Autoplaten die-cutter
To support the companys strategy, MPS Leciester invested in NOVACUT 106 ER Autoplaten die-cutter for in-line blank separation from BOBST. The machine drives flatter, more consistent blanks straight into the finishing process and removes the need for hand stripping and blanking, for all but the smallest jobs.
Capable of processing 8,000 sheets per hour, NOVACUT 106 ER has automatic in-press blank separation capabilities that deliver the correct combination of force and finesse required to blank sheets precisely. When blanking is not a prerequisite the NOVACUT 106 ER can be set up to operate as a full sheet delivery machine in minutes, therefore having dual capabilities of traditional waste stripping when required, along with blanking, without limiting the machine to one process or the other.
Functions such as continuous pile lowering, constant batch compression and automatic tie-sheet insertion ensure perfectly stacked piles, while the modular non-stop grid allows the highest productivity levels. Digital centering means that small variations in the tools can also be quickly and easily adjusted on-press.
Craig McGowan, BOBST Area Sales Manager, commented: “Its been really interesting watching the process MPS has adopted in investing in automated blanking. Historically, many companies have believed that the cost of automating far outweighs the savings made, compared with hand stripping and blanking, and that it can only be used for long run, large format work to be cost effective.
“This simply isnt true anymore. With the developments being made in blanking tools ensuring they are more cost competitive, converters can now utilise blanking technology for short run, small format jobs. And when blanking isnt required, a full sheet delivery system is available allowing MPS production without bottlenecks.”
Impact & results
Mark White, MPS Leicester Operations Director, continued: “Our expertise and in-depth understanding of our customers needs, from speed of turnaround to security, traceability and specific pack data requirements, allows us to make continuous operational improvement. We are committed to investing in future-proofing our production and ensuring 100% compliance at all times. The systems and technology we have in place at Leicester ensure we are going the extra mile to de-risk our business.
“The recently installed machine, which drives flatter, more consistent blanks straight into the finishing process, not only offers benefits in terms of de-risking but has also significantly increased the number of jobs that can be run at full speed, allowing us to set the benchmark for quality in the industry. NOVACUT 106 ER has become critical to our operation minimising make readies and driving efficiency.”
Craig McGowan, BOBST Area Sales Manager, added: “With many cut & crease and gluing lines and now including the new BOBST NOVACUT 106 ER working across all formats, MPS Leicester has the ability to grow; yet more importantly, has the technical skills and technology to over-deliver and secure a successful future under its new WestRock ownership.
“At MPS we see a machine running at the speeds promised, being used for large format, as well as short run jobs down to less than 1000 sheets, and still achieving setup times of around 30 minutes. This means the NOVACUT is in continuous use and adding 5-10,000 additional cartons per hour to the gluing lines enabling great service for the shorter run, higher frequency demands from customers. A great result for the site.”