Offset Printing
Environmental Protection: Heidelberg Presses Exhibit Low Energy Consumption
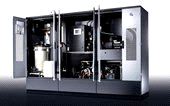
Wednesday 15. July 2009 - Practical tests show that the Speedmaster XL 105 with coating unit and dryers consumes between 10 and 20 percent less energy than comparable systems; Peripherals play a key role in the energy balance; Considerable difference between energy consumption and connected load
In times of climate change, increasing CO2 emissions and rising electricity costs, the energy consumption of a press is becoming an increasingly important factor. Although energy costs only account for between two and three percent of the production costs of a print job, the connected load of a new press scares off many print shops.
In the last few months, Heidelberger Druckmaschinen AG (Heidelberg) has been performing comparative measurements on various makes of press to provide greater transparency of the energy consumption and thus the CO2 emissions of its presses. To this end, Heidelberg processed an identical job on each press using the same ink, printing stock and production speed and measured the energy consumption, including all the peripherals, such as those required for cooling and air supply. This equipment often accounts for half the energy consumption.
The comparison showed that, at production speeds of between 14,000 and 18,000 sheets per hour, the Speedmaster XL 105 was the B1 press with the lowest energy consumption. Without drying, the Speedmaster XL 105 uses between five and ten percent less energy than all the other competitors featured in the comparison. With a coating unit and IR and hot-air drying, this figure climbs to between ten and 20 percent. And this was the case even though the maximum connected loads of some Heidelberg presses are higher than those of its competitors. This clearly demonstrates the flexibility and reliability in production that Heidelberg offers its customers, particularly with round-the-clock production at speeds of 18,000 sheets an hour.
There are many reasons for the energy-saving success of the Speedmaster XL 105. Heidelberg has been investing in sophisticated control technology for many years. For example, AirStar – the air supply for the press – is almost twice as efficient as the next-best system on the market thanks to its unique turbo radial blower and the use of frequency control for all air generators. In terms of inking unit temperature control, the CombiStar Pro, which is available as an option, can be used to minimize the output of the cooling unit in spring, fall, and winter. The biggest difference is achieved with the drying process. The DryStar dryers, which are developed in-house, are located closer to the sheet and work at a higher air speed, which reduces the power losses during the drying process considerably.
Peripherals play a key role in the energy balance
A whole host of other consumers are required in addition to the press itself – dryers, the dampening solution supply system, inking unit temperature control, air supply and compressed air. At Heidelberg, these peripheral systems are powered via the press, which means they are already included in the connected load. Many importers, on the other hand, supply these devices locally, which means they are not initially included in the press specification. This is why the connected load of their presses appears to be lower. This factor is crucial, because peripherals can account for up to 50 percent of the connected load and the energy consumption. Often, manufacturers compare presses with and without inking unit temperature controls. With an eight-color press, this can account for up to 20 percent of the energy consumption.
Considerable difference between energy consumption and connected load
The energy consumption of a press is not as easy to calculate as that of a domestic light bulb or a PC. It is important that the energy consumption is not confused with the connected load. The connected load describes the peak power level that the press can handle at maximum load. This is the value that would be reached if all the following criteria were met – startup in a cold climate, simultaneous use of all the functions, maximum area coverage and coating application, the highest press speed, and the thinnest printing stock available. Most print shops never reach this value. To ensure full flexibility in operation, Heidelberg specifies this value in its technical data and recommends that customers configure the transformer and lines accordingly.
Energy consumption, on the other hand, describes how much energy the press requires for a specific print job. To determine the cost of the electricity, this consumption must be recorded and averaged over a period of several months and must also take into account the makeready times. As a rule, the average value comes to between 40 and 60 percent of the maximum connected load, depending on the print shop’s product range and the press environment.
Heidelberg is committed to environmental protection
Environmental protection has been an integral part of Heidelberg company policy since 1992. In 1996, the foundry in Amstetten was the very first site operated by a press manufacturer to be granted an eco-certificate. Environmental management systems to ISO 14001 are now in place at all sheetfed offset sites. Besides its own production, the company focuses on developing innovative, environmentally friendly presses. For example, the new Speedmaster XL 105 has increased productivity by 30 percent with the same, and in some cases even lower, energy consumption. Key peripherals in the Star System have also been developed to reduce the environmental impact of the printing process, for example the PowderStar AP 500 and CleanStar for lower powder application and dust levels, or the new FilterStar and FilterStar Compact for reducing energy consumption. Heidelberg uses the Print Media Academy to help its customers put eco-friendly printing principles into practice.
Heidelberg announced its HEI ECO Printing Award at drupa 2008, and the winners were honored in the spring of this year. This award provides customers with a platform for passing on and discussing their good ideas. This knowledge, along with a great deal of information on all aspects of sustainability, is available on the Heidelberg website in a section dedicated to the environment.