Offset Printing
KOMORI LAUNCHES NEXT GENERATION LS TECHNOLOGY AT DRUPA WITH LITHRONE SX40
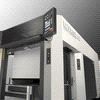
Thursday 10. April 2008 - At Drupa 08, Komori will introduce the Lithrone SX40, the latest evolution of the world renowned, award winning LS platform. The LSX40 features a host of upgraded features, designed to further improve print quality and job cycle times.
The Lithrone SX40 has a new maximum running speed of 18,000sph. In addition, new higher speed fully automatic plate change (F-APC) with non stop plate removal, helps increase the speed for job to job changeover, essential for busy print houses handling various run lengths. The Lithrone SX40 can change six plates in approximately two minutes, enabling, along with KHS-AI, a 35% reduction in job-to-job-changeover time. From the end of production on one job to an OK sheet on the next it takes just over six minutes. The automated coater plate change increases speed, precision and ease of use. All controls are integrated and automatic through the new PQC consoles touch screen. The new KHS-AI fast print start-up system has a self-learning function which progressively updates all press settings.
Changes to the feeder
*The feeder on the new Lithrone SX40 has been developed for higher speed and to optimise the benefits of the new KHS-AI fast print start system.
*The feeder board now requires no wheels for most jobs and has an independent motor – not driven by the press, so sheet arrival timing can be adjusted electronically – which enables greater control now that the press accelerates towards maximum speed faster.
*The front lay area has been modified in order to improve handling of lightweight materials – especially at maximum press speed.
*Within the feeder head mechanism, the cam follower drive has been modified to maintain constant contact at the highest speed. This ensures a highly accurate sheet separation and transfer with minimum maintenance.
*On top of the feeder pile is an air containment system that allows precise sheet transport with the minimum of air, even when feeding at the higher maximum speed.
*The number of front lays has been increased and the air control has been modified in the sheet infeed area to ensure precise register at this higher running speed.
Changes to the printing units
*The water flow in the damping system has been improved to stabilise damping solution temperature and maximise the benefits of alcohol free printing.
*The ink fountain has been strengthened and the cheeks are now made of solid brass to ensure zero-set positioning in all operational temperatures – essential in order to maximise KHS-AI.
*The fully automatic plate changing system (F-APC) is new – now enabling non-stop continuous plate removal – and reducing the changeover time for six plates to approximately two minutes.
*The automatic impression cylinder cleaning device has been repositioned underneath the cylinder, freeing up more space and providing more flexibility in locating interdeck driers and additional air guides which are often beneficial to the higher speed running of heavyweight carton stock.
*Blanket washing speed is increased through the new wet cloth system, with blankets and rollers now washed simultaneously and at the higher cylinder revolution speed of 8,000sph.
*Transfer cylinders are of the contact free, skeleton type – with a new venturi system – to create a “virtual cylinder of air”. This is independently controlled via the pre-set air control system which is integrated into the KHS-AI programme and its settings are progressively updated through KHS-AIs automatic intelligence function.
*The transfer cylinder is diagonally skewed improving unit-to-unit registration accuracy, and enabling the image on the coating units blanket cylinder to be skewed – useful when precision spot coating.
*The coating unit has several new innovations, including automated plate changing, automated varnish circulation, automated blanket and coater impression cylinder cleaning. Furthermore, all these washing programmes are now integrated into the KHS -AI programme.
Changes to the delivery to accommodate the sheets higher travelling speed
*The delivery profile is higher – which improves coater dryer and maintenance access, and means that the sheet is flat when it reaches the final delivery vacuum system. At higher paper speed, this also provides additional sheet control and longer drying time.
*More variable speed blowers have been added in the delivery and are now integrated into the pre-set and self-learning functions of KHS-AI.
*The delivery gripper bars are of a new shape to reduce the delivery air pressure and reduce air turbulence in the delivery.
*In the delivery pile, the diameter of the vacuum slow down wheel has been modified to provide greater sheet control.
Emission levels on the Lithrone SX40 are so impressive that the new press has attained the very important environmental BG certificate even before launch. To comply with the necessary BG standards, the press needed to prove its capability to reduce an extensive range of waste emissions, run alcohol free and produce acceptably low noise levels.
Visitors to Drupa will be able to witness the Lithrone SX640 + Coater in action. Komori will be running over 30 live demonstrations every day on a range of presses on its 2,000 m” stand in Hall 15.